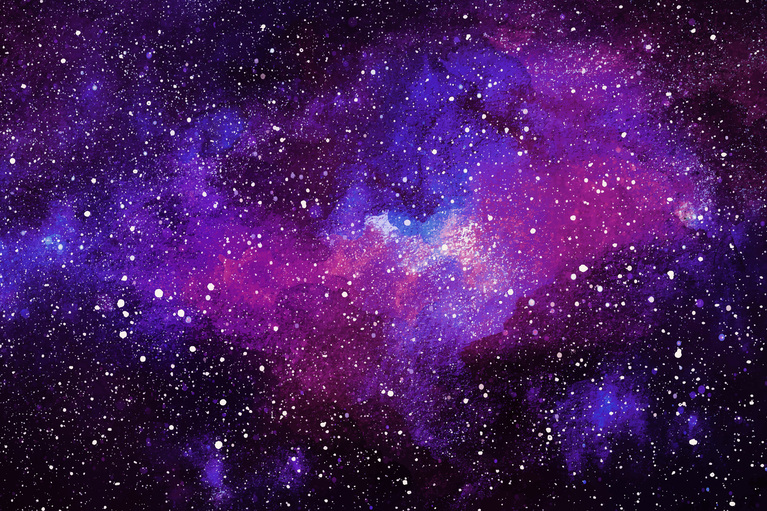
Microgate and Vicor partner to unlock deep space secrets
Learn how high density power modules help colossal Earth-based telescopes enhance deep space images
Wafer-level automated visual inspection systems ensure the highest quality and reliability of semiconductor ICs and enable manufacturers to continuously improve yields. These systems employ precision optics and analog circuitry to identify the smallest defects during wafer fabrication. As lithographic dimensions continue to shrink with advances in the latest process nodes, manufacturers require the highest defect sensitivities.
This requirement places stress on the analog and mixed-signal circuitry in vision systems that require considerable noise filtering. As power needs increase, filters are becoming too large to be accommodated by these systems. A new approach to power delivery is required to keep pace with advances in semiconductor wafer fabrication.
Automated vision system design engineers can reduce noise in sensitive wafer inspection systems starts with a reconsideration of the power delivery network. A critical first step is moving the system from an outdated 12V bus to a more power-efficient 48V bus to improve efficiency and thermal issues. However, to fully achieve wafer inspection requirements, it is necessary to employ a solution that is inherently low-noise. Vicor BCM fixed-ratio converters with sine amplitude conversion (SAC) topology mitigate noise and allow manufacturers to use less filtering. As an added bonus, the compact size and low profile simplifies thermal management that, in turn, simplifies the mechanical design of inspection systems.
Isolated fixed-ratio
Input: 800 – 48V
Output: 2.4 – 55.0V
Current: Up to 150A
Peak efficiency: 98%
As small as 22.0 x 16.5 x 6.7mm
Microgate and Vicor partner to unlock deep space secrets
Learn how high density power modules help colossal Earth-based telescopes enhance deep space images
Power modules enable world's most advanced all-electric work-class ROV (eWROV)
Saab UK introduces versatile, environmentally-friendly eWROV that achieves world class performance using compact, thermally-adept power modules
Powering Innovation eBook: Volume 1 – Saving the environment
Technological breakthroughs to protect and preserve the environment
Powering Innovation eBook: Volume 2 – Protecting and saving lives
Innovative solutions that protect and deliver lifesaving materials and services