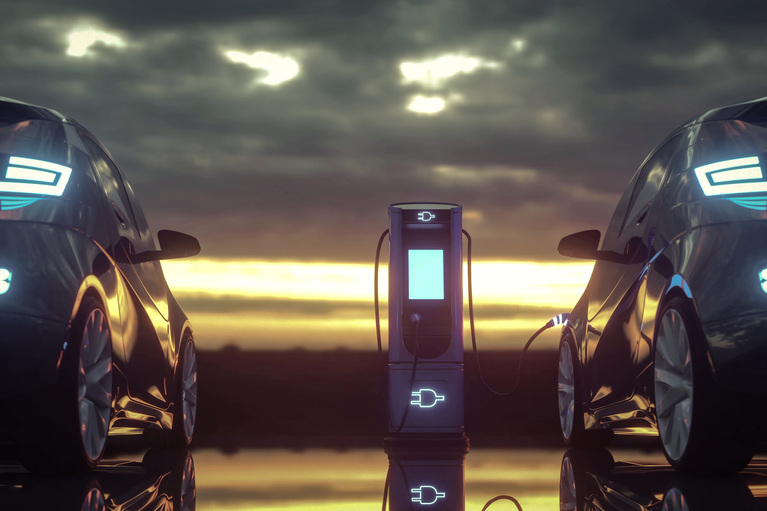
High-bandwidth power modules quell the disruption of high-voltage line ripple rejection
Vicor DC-DC converters combine high bandwidths with soft switching topologies to reduce EV ripple rejection more effectively than conventional solutions
White Paper by Joe Dussi, Senior Regional Marketing Manager
When evaluating the option to use a power module or a discrete power solution, there are a number of important design variables to consider as well as other ancillary functions that impact the overall power delivery network (PDN) design process.
To start, you need to determine if you have the necessary in-house power design expertise to design, evaluate, test and manufacture a discrete power solution. In most cases, companies do not have the luxury of employing a dedicated team of experienced power design engineers because it is just too costly. In addition to the obvious economic implications, there are many performance and design advantages to using a sourced power module over a home-grown discrete solution.
Taking it one step further, not all power modules are created equal. Innovative and patented Vicor power module technologies incorporate advanced topologies, miniaturization and thermally adept packaging. The combination of these design techniques enables power modules with greatly reduced magnetics and much higher power density and efficiency at higher frequencies as compared to alternative power-modules or discrete-designs. This proven technology has been powering growth markets such as data center, automotive, robotics and more. The following matrix (Table 1) offers a high-level comparison of the differences between Vicor power modules and discrete power solutions.
Discrete power solutions are inherently inefficient to design and manufacture because they require a larger footprint to accommodate the increased bill of materials (BOM) and the circuitry necessary to connect the individual components. In most designs, discrete solutions only utilize one side of the printed circuit board (PCB), which means even a bigger PCB as shown in Figure 1.
Figure 1: Vicor power module designs are smaller than most discrete power solution alternatives.
Vicor PI3740
PCB Size: 2.0 x 2.375in
BOM count: 31
Key device: 10 x 14mm DC-DC regulator
Efficiency at 12V: 95%
2 FETs and 2 Diode
PCB Size: 4.3 x 3.55in
BOM Count: 42
Key device: 6.4 x 4.4mm TSSOP20
Efficiency at 12V: 87%
On the other hand, power modules maximize the available design space by using both sides of the integrated PCB resulting in a much smaller footprint and increased power density as illustrated in Figure 2.
Figure 2: Illustration showing the inside of power module demonstrating the efficient use of space resulting in a much smaller and power dense solution.
Figure 2: Illustration showing the inside of power module demonstrating the efficient use of space resulting in a much smaller and power dense solution.
Beyond the obvious physical advantages, modules offer designers a variety of improvements in performance. Because of their compact size and specialized topologies, modules have a higher power density and in most cases are more efficient, meaning you can design a power delivery network that drives more power in less space (Figure 3). This comes in handy when faced with design envelopes that are limited in volume and require a PDN capable of delivering the power needed to support a mission-critical application in challenging environments like space or under the sea. With Vicor power modules you don’t need to sacrifice power because of space limitations or, conversely, add space and weight to accommodate more power. You can still have the power you need (and more) using the existing power footprint. In contrast, discrete solutions need to be significantly resized to account for the additional power requirements.
Figure 3: A visual representation demonstrating the size and space advantages of using a Vicor power module.
Figure 3: A visual representation demonstrating the size and space advantages of using a Vicor power module.
When using Vicor power modules, you don’t have to live in fear that you may need to redesign the PDN from scratch to accommodate more (or less) power. There’s no need for costly and lengthy power redesigns that will set your project back months. Scaling through re-use of prequalified modules eliminates additional testing and recertification, as well as additional work to source the new BOM. Modules provide the flexibility and scalability needed to make design changes quickly and efficiently with minimal design involvement — saving you both time and money, and meaning faster time-to-market.
Individual modules perform the needed conversion at each load
Individual modules perform the needed conversion at each load
If power needs change, a module is replaced with a suitable power module
If power needs change, a module is replaced with a suitable power module
If an additional load is added, another module is added
If an additional load is added, another module is added
To reduce losses, one module is used for regulation and one for transformation
To reduce losses, one module is used for regulation and one for transformation
To quickly double the power at a load, add a second module
To quickly double the power at a load, add a second module
With a high voltage power source, a module is added to create a SELV bus
With a high voltage power source, a module is added to create a SELV bus
The fundamentals of thermodynamics state that the most effective and efficient way to transfer (remove) heat from a heated substrate is to maintain a uniform and consistent flow of fluid (air or liquid) across that surface (laminar flow). To do this you need to have a heat sink profile that minimizes or eliminates any abrupt variations in that surface that could potentially change the flow from laminar to turbulent, thereby reducing thermal transfer efficiency.
This theory can be directly applied to the Vicor-module-versus-discrete comparison. As previously discussed, power modules are very compact and have a higher power density than discretes, which means they could have a higher localized heat signature than a discrete solution. At first you may see this as a win for discretes, but that is not the case. As shown in Figure 4, power modules have a physical profile that supports laminar flow, thus removing heat quickly and efficiently. In a discrete solution, however, heat losses are not isolated to one spot. Rather, they are scattered throughout the design, making it more difficult to cool. Adding to this challenge, the physical form of a discrete solution is chaotic: the profile of a discrete solution looks like a cityscape with many peaks and valleys, and therefore does not support laminar flow. The discrete solution’s inherently varied topography promotes turbulent airflow which can lead to excessive localized heating.
Figure 4: Vicor’s packaging profile allows for a uniform and predictable heat dissipation while the discrete solution results in uneven and unpredictable heat dissipation.
Figure 4: Vicor packaging profile allows for a uniform and predictable heat dissipation while the discrete solution results in uneven and unpredictable heat dissipation.
To learn more about Vicor innovative high-performance power module packaging, read the white paper by Phil Davies, Senior Vice President at Vicor.
We’ve all seen videos of pick-and-place machines frantically placing parts on a printed circuit board at high speed. Less visible are the many complex systems that make this advanced manufacturing technique possible. Each of these fine-tuned systems has a narrow margin for operation at peak efficiency. The slightest malfunction in a subsystem could be catastrophic, and at speed, an operator will not notice until it is too late. There are hundreds or even thousands of electrical solder connections on a PCB, depending on the complexity of the finished design as illustrated in Figure 5. Basic statistical analysis theory shows that the odds of a failure increase with every additional connection.
Keeping that in mind, which power design would be less likely to experience a failure due to a manufacturing error? The power module design. There are far fewer connections that need to be made than in a discrete design, making it less prone to quality defects during assembly. With fewer placements, there is also less need for multiple assembly stages. This reduces the number of times the board is handled by operators, thereby reducing the potential for electrostatic discharge (ESD) damage during the assembly process. All of this translates into greater reliability.
Figure 5: With hundreds of components with multiple connections making up thousands of individual connections your odds increase exponentially for having higher assembly defects in a discrete design.
Figure 5: With hundreds of components with multiple connections making up thousands of individual connections your odds increase exponentially for having higher assembly defects in a discrete design.
When choosing between a power module and a discrete design you need to take a step back and consider not just the design but the overall life cycle to understand the full benefits of the modular approach. As shown in figure 6, in the case that you chose to design your own power delivery network using discrete components, your own in-house power design group would shoulder the whole burden of design, test and validation for every power system.
Figure 6: A simplified design lifecycle timeline illustrating the advantages of using a module solution versus a discrete solution.
Figure 6: A simplified design lifecycle timeline illustrating the advantages of using a module solution versus a discrete solution.
After the design was validated by your design team you would need to have it tested again in order to be certified by a third-party agency to ensure it meets all required certifications (UL, CE, UR, etc.). Once certified, you would need to work with your own manufacturing group or a contract manufacturer to create a manufacturing plan. Once you are sure the manufacturing process is complete, which includes final test, then you would need to engage with the sourcing department to start the long process of sourcing negotiations and contracts for all of the individual components on the BOM. Many of these components might also require a second source, making procurement that much more difficult. With all these moving parts and dependencies on multiple vendors in your supply chain this introduces the very real potential for mistakes or unplanned interruptions leading to greater risk. Additionally, if the design ever needs to be scaled up, everyone goes back to the drawing board.
On the other hand, if you were to base the design on power modules, you would source pre-qualified power modules from Vicor and use a small number of discrete components to complete the design. This would make the supply chain logistics much easier and less stressful on your organization. You would also be assured that each module you received was thoroughly tested and came with the appropriate QC approval from the vendor. To top it all off, as power requirements increase (they always do!), you would be able to reuse more of the same modules to obtain more power, removing the most painful parts of the re-design process.
For additional information on how Vicor power module products can help you design the optimal PDN solution, go to www.vicorpower.com/innovation. While there explore our technical resources and online design tools available 24/7.
High-bandwidth power modules quell the disruption of high-voltage line ripple rejection
Vicor DC-DC converters combine high bandwidths with soft switching topologies to reduce EV ripple rejection more effectively than conventional solutions
The future of standardized defense platforms using MOSA, SOSA and VPX open architectures
Using open standards to increase interoperability, scalability, reliability, reduce system costs, and minimize the number of custom electronics designs
Delivering higher power density and low noise for New Space applications
Patented power design techniques and architectures needed to deliver optimal power and low noise for space communications applications
Optimizing high-density power design: modular vs. discrete
There are several important design variables to consider when evaluating the power module design process