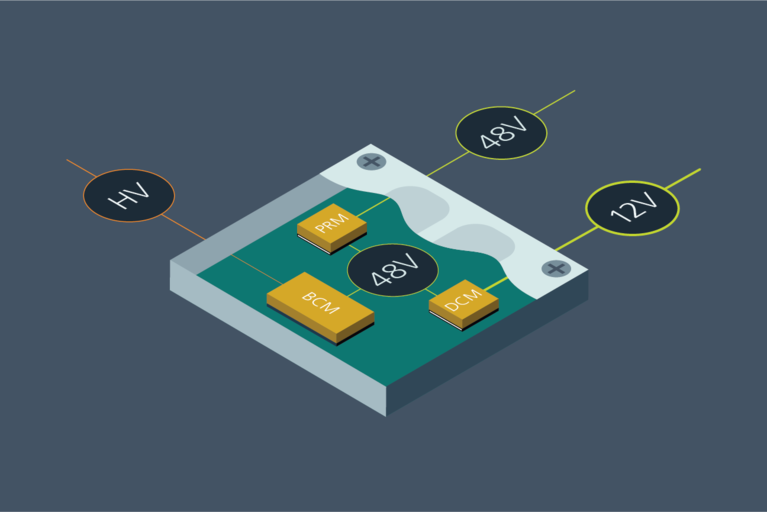
高密度功率模組簡化和縮小電動汽車電源系統設計
Vicor 電源模組為電動汽車應用注入創新。瞭解三款汽車級新產品將如何徹底改變未來的電源設計
It’s not surprising that when you’re developing leading-edge power components you can’t just purchase all the test equipment you need off-the-shelf. Commercial systems can’t deliver all the comprehensive, accurate data required for documenting the actual performance of all parameters of device performance. So Vicor devotes a team of engineers – and a significant budget – to developing test equipment to help engineers and ensure outstanding quality of all the products leaving their production lines.
A core element of these tools is the design introduction verification analysis (DIVA) software, developed by Vicor to analyze and compare units and groups of units to generate specifications for the factory to ensure that at high volume production, units have acceptable CPKs (process capability index).
This specialized test equipment gathers sufficient data to establish that the product works to spec., design requirements are met, data sheets are accurate and that the company’s Whiteboard, which is a tool that simulates how Vicor products behave under all conditions, is loaded so that customers and FAEs get a clear and accurate view of the device performance.
The software and hardware used to examine every production part is almost an exact duplication of the design engineering ATE, so that production test routines are a subset of those used in engineering. This ensures that the performance of production parts doesn’t deviate from the data sheet specifications.
In manufacturing, all tests are made up of comprehensive functional measurements; the high density of these products means that there is just no space for conventional test points. This means that real-world testing of all parameters, at all loads, and at temperatures from as low as -55°C and high as 100°C is carried out on each device.
Vicor uses a universal software for test and analysis (USTA) tool which was designed and developed entirely in-house and allows engineers to simply fill in blanks on routines that have already been built; this is much faster than writing VB, Labview, etc. This also creates a consistency of testing from one product to another because the same USTA engine is used on disparate ATE hardware configurations, ensuring consistency throughout the whole test process.
The intensive focus on innovative test equipment allows for high yield and high mix production. Operators do not have to make the decisions on how to test; the company’s CIM system does all of this. Even the defined order of temperature testing (e.g. low, mid & high temp) is fixed; i.e. the operator cannot test high temperature first if the specification requires low-temperature testing to be carried out first.
Most high volume lines involve automatic handling. All devices have an assigned unique serial number so that Vicor – and importantly, customers – can access actual test data for individual units; a valuable facility that has been available for customers for many years, especially impressive when the company currently tests over 20,000 devices per day.
It’s not common practice for a power supply company to invest in this high level of testing; with Vicor it is more like a semiconductor manufacturer’s process giving full traceability for individual devices and is a huge confidence-building factor for the customer as well as an important differentiator for Vicor.
In addition, the large test engineering department with several test engineers in the design engineering department and a skilled IT team to support the processes speed up the verification of manufactured units. The company’s PCB layout, mechanical design and robot handlers for products represent a significant investment. Customers value and benefit from this intensive testing.
Data Acquisition Test Setup
高密度功率模組簡化和縮小電動汽車電源系統設計
Vicor 電源模組為電動汽車應用注入創新。瞭解三款汽車級新產品將如何徹底改變未來的電源設計
高密度電源模組推動主動懸架技術日趨成熟
主動懸掛系統已從 20 世紀 90 年代的測試版發展成為今天的 48V 驅動系統。瞭解電源模組對電源系統設計的影響
基於 MHz 開關頻率的器件助力實現 DC-DC 轉換器和 EMI 濾波器的小型化
想像一下,使用 DC-DC 轉換器解決方案來利用高頻開關的優勢,而不會發生傳統解決方案的缺點
採用 48V 區域架構,打造面向未來的先進電動汽車
隨著原始設備製造商(OEM)採用 48V 電源架構,他們正努力優化其電源系統設計。 Vicor 的高功率密度模組可為 48V 區域架構提供峰值效率