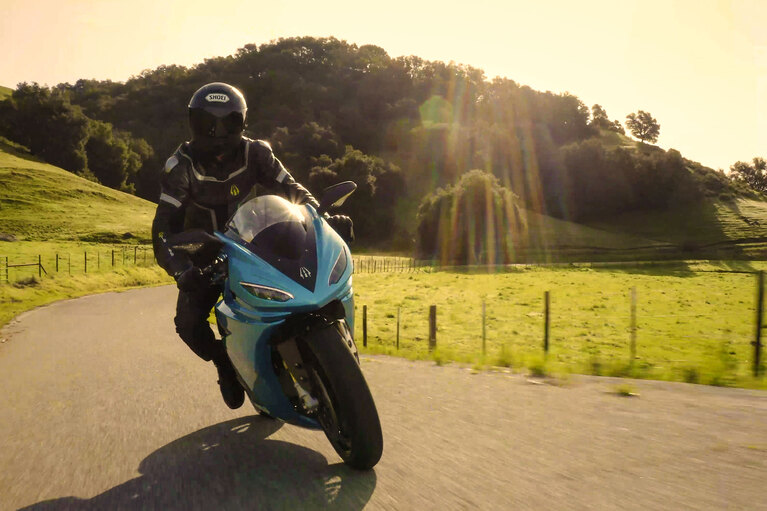
从派克峰到 Bonneville 盐滩,Lightning 的速度超越内燃机摩托车
Lightning Motorcycle 设计的电动摩托车在各个领域都表现出色。了解 Vicor 电源模块如何支持下一代摩托车的详情
探究高密度双向 DC-DC 转换器模块如何在不断发展的电池生态系统中扮演关键角色,加速循环周期、提升能源效率并降低运营成本。
作者:David Krakauer,全球市场营销副总裁
电气化在众多行业持续普及,不仅提升了生产力,还带来了环境优势,而电池生产是这一趋势的核心技术推动力。受电动汽车(EV)和可再生能源储能系统的推动,电池行业已成为全球增长最快的行业之一。
国际能源署(IEA)的数据显示,全球电池需求从 2016 年的每年 43.8GWh 激增至 2022 年的每年 550.5GWh,增长了十倍。随着需求的不断增长,电池生命周期的每个阶段都值得我们深入探究。整个电池生命周期分为四个主要阶段:电池化成、电池测试、应用和回收。任何阶段的短板都可能阻碍电池行业的发展和电气化的普及。现有的电源转换技术不利于电池生命周期的发展,成了阻碍市场前进的障碍。Vicor 开发的高功率密度固定比率转换器技术,带来了一种创新的方法,可以在电池生命周期的各个阶段提升可持续性和成本效益。
在高压电池系统中,DC-DC 电源转换是供电架构的一个基本方面。DC-DC 转换通常通过开关模式电源转换器(如降压或升压拓扑)或低压差稳压器(LDO)实现。这些电源转换器可能有效,但它们的输出刚性和较低的转换效率限制了供电网络(PDN)的灵活性和性能。目前,电池系统的高电压凸显了这一不足。为了克服这些缺点,Vicor 开发了固定比率转换器,在小巧的封装中实现了高效的隔离转换,适用于从高压到低压(通常称为安全特低电压(SELV))的负载转换。类似于 AC-AC 解决方案中的变压器,固定比率转换器用于执行 DC-DC 转换,其输出电压为输入电压的固定分数(见图 1)。变压器的降压或升压能力由线圈匝数比定义;同样,固定比率转换器的转换能力取决于其 K 因数——K 因数为相对于其降压能力的比例(见图 2)。
图 1:双向固定比率转换器既可作为降压转换器(K=1/12)运行,也可以作为升压转换器(K=12/1)使用。这种单一模块中的双向转换功能为电池行业创造了前所未有的应用场景。
图 2:Vicor 的 BCM 固定比率转换器支持多种不同的 K 因数和输出功率配置,可以满足大多数应用的需求。
传统 DC-DC 转换器调节输出电压,而固定比率转换器则不同,它不提供输出调节。这些设备还可以自主运行,不需要环路反馈或外部控制机制。与传统转换器相比,固定比率转换器具有几方面的明显优势。
固定比率转换器的运行独立于外部主机或控制器,因此本身具有双向转换功能。也就是说,根据电流流动方向,只需一个转换器模块即可完成升压和降压。因此,固定比率转换器可以为依赖双向电流流动的供电网络(PDN)带来前所未有的灵活性和简便性。
固定比率转换器易于并联,可以满足更高的功率需求。设计人员可以轻松添加多个固定比率转换器模块,将它们并联起来,扩展系统以满足所需的输出功率需求。同样,设计人员可以串联多个固定比率转换器,根据其级联 K 因数实现独特的电压转换比。在这些情况下,转换器需要功率匹配以确保安全可靠的运行。
最后,固定比率转换器在小巧的封装中实现了卓越的电源转换效率。传统的降压或升压转换器的最大转换效率只有 90% 左右,而 Vicor BCM® 系列的固定比率转换器的转换效率接近 98%。这不仅提升了应用的可持续性,还大幅降低了热管理开销。
电池生命周期的第一个阶段是电池化成。在该阶段,新生产的电池必须经历化成循环过程,即首次对电池电芯进行充电和放电操作。在此过程中,电池进行多次循环,逐渐形成固体电解质界面(SEI)层。该过程的速度取决于电池电芯的化学性质,因此电池化成的用时大多是固定的。
电池化成循环需要一个能够支持重复充放电循环的底层供电网络(PDN)。
在这种情况下,普通 PDN 从电网获取三相交流输入,将其整流为高压直流电,然后通过多级 DC-DC 转换达到为电池电芯充电所需的标称电压(例如 4.2V)(见图 3)。为电池充电所需的最终电压因电池而异,具体取决于电池电芯的化学性质,但在将交流电转换为较低直流母线电压(例如 12V)时,使用几个中间电压降是全行业的标准做法。
图 3:电池制造商可以使用固定比率转换器,将双向转换功能集成到电池化成供电网络中,同时提高效率。
分立式组件解决方案的设计非常困难,需要企业具备全面的内部电源技术专长,而且物料需求大。这不仅会增加成本,带来供应链挑战,还会延缓产品上市时间。分立式解决方案会限制灵活性,因为它们只能提供预定义的输出电压。由于电池的化学性质不同而需要不同的电压时,如果设计人员能够创建一种可以根据电池的具体化学性质进行修改的灵活解决方案,则更加经济高效。使用分立式解决方案时,电池化成系统缺乏灵活性,无法动态修改以兼容多种电池类型。
现有电池化成供电网络面临两大挑战:吞吐量和效率。
从吞吐量角度来看,制造商对电池的 SEI 层进行化成的速度本身受限于电池的化学性质。因此,若想提高电池化成过程的经济高效性,需要能够并行化成多个电池的可扩展系统。然而,现有的供电网络缺乏模块化的中间 DC-DC 转换阶段,在不进行大规模设计修改的情况下无法轻松扩展系统。
从效率角度来看,对电池进行连续充放电的成本很高。为了优化效率,电池制造商需要重复利用电池充电过程中消耗的能量,要么将其存储在本地,要么在放电过程中将其送回电网。这就要求供电网络能够支持双向电流流动并高效地完成电源转换。
在这两种情况下,固定比率转换器都是理想的解决方案。通过将固定比率转换器集成到供电网络中,设计人员可以将架构重新定义为三个不同阶段:交流电整流、低压转换和恒流转换(母线转换器)。
在恒流转换阶段,设计人员可以利用固定比率转换器,轻松地将较高的直流电压降至更安全、更低的电压,而无需分立式解决方案或单模块解决方案。通过并联一个或多个固定比率转换器,他们就可以创建易于扩展的模块化供电网络。
这样,设计人员就可以设计出同时循环多个电池的系统,从而实现更高的吞吐量、功率密度和效率。此外,这种架构还允许设计人员轻松更改 PDN,根据电池的独特标称电压完成所需的 DC-DC 转换。无需分立式组件,解决方案更加灵活,就可以加快产品上市速度并降低故障率。
在节能方面,固定比率转换器固有的双向转换功能在电池化成过程中尤为有效。使用固定比率转换器,电池制造商就可以在充电和放电循环之间自如切换,因为他们知道固定比率转换器将在放电时自动升压到预定义的较高电压,在充电时进行降压。这一独特功能可提高化成过程的能效,在化成循环期间重复利用能源。
此外,固定比率转换器的效率高达 97.9%,双向转换过程中的功率损耗微乎其微。如果没有固定比率转换器,将需要多个组件(一个用于降压,一个用于升压)才能实现这种双向转换功能。这样就会因为效率低下而消耗更多功率并增加组件数量。
电池生命周期的第二个阶段是电池测试。在此阶段,制造商将电池电芯组合成更大的电池组。电池电芯的充放电受限于一些时间要求(取决于化学性质),而电池组的生产则不受这些限制,但仍面临同样的吞吐量挑战。
例如,每个电芯都必须经过适当的测试并进行精确的测量,以确保多个电芯能够组成更大的电池组。然后,更大的电池组也需要经过严格的测试。这不是一个增值步骤,因此制造商完成这一步骤的速度越快,电池组的整体成本就越低。
为了适应各种电池电压和功率水平,供电网络必须灵活而且可扩展。同时,为了在相同的物理空间内以更短的时间测试更多电池,需要供电网络提供高吞吐量。因此,电池组测试设备需要模块化且可扩展的供电网络,以满足具体的测试要求和测试量。与电池化成阶段一样,电池测试设备的标准供电网络也需要将三相交流电转换为电芯的标称电压(见图 4)。
图 4:固定比率转换器为电池测试供电网络带来高功率密度,通过在相同空间内安装更多测试设备来提高测试吞吐量。
在供电网络的恒流转换阶段使用固定比率转换器,电池测试设计人员就不再需要费力地设计中间转换阶段。相反,他们可以放心地利用固定比率转换器来管理恒流转换。这样,他们就可以专注于转换过程的最后阶段,即将电压与电芯的标称电压相匹配以进行测试。这种简化的架构使设计人员能够创建灵活的模块化系统,并根据不同的测试要求轻松进行修改。
固定比率转换器的另一个重要优势是功率密度。凭借极高的功率效率和小巧的外形尺寸,固定比率转换器可以在行业领先的小巧设计中支持数千瓦的功率和数百伏的电压。这样就可以构建吞吐量更高的测试仪,在相同的空间内安装更多测试设备,从而为同步测试更多电芯创造机会。
当电池最终出厂并投入实际应用时,供电网络的挑战并未结束。
在许多新兴的电池供电应用中,如系留机器人或水下机器人(ROV)、太阳能和风能等可再生能源储能系统以及电动汽车,对极高电压供电的需求不断增长(见图 5)。例如,为了增加功率,提高效率,电动汽车的供电架构正从 400V 过渡到 800V。
图 5:系留机器人等应用可以使用固定比率转换器实现高压供电,而不会在转换为低压的过程中产生显著的功率损耗。
在相同的功率下,电压越高,供电电流就越小。因此,高压供电的一个优势是效率更高,因为更小的电流可以减少 I2R 损耗。这使得应用更加高效,同时也减少了热管理消耗。
此外,高压供电可以减小车辆线束的线规。由于供电电流更小,设计人员可以使用线径更小的电缆,从而减轻系统重量,降低材料需求和成本。
显然,要使这种高压系统成功运行,需要将这些用于供电的高压转换为负载点上使用的低压。在电池生命周期的这个阶段,固定比率转换器通过提供一种简单而高效的直流电源转换手段来提高价值。
以系留机器人为例,利用 K 因数为 1/16 的固定比率转换器,设计人员能以 97.9% 的效率,将电压从用于供电的高压(例如 800VDC)降至较低的电压,例如 48VDC。在 48VDC 的基础上,设计人员可以使用效率为 90% 的常规降压转换器,获得微控制器单元(MCU)最终所需的 3.3V 电压。如果没有固定比率转换器,从 800V 到 3.3V 的整个转换过程将以 90% 的效率进行,产生的损耗将显著高于固定比率转换器架构。
电池生命周期的最后一个阶段是回收。
电池回收是一个高功率的电化学过程,通过化学手段将电池中的原材料和元素分离出来,以便将来进行回收和再利用。与电池生命周期的其他工业阶段一样,供电网络需要将三相交流输入电压转换为高功率直流电,最终降至较低电压,为回收设备供电(见图 6)。
图 6:BCM 固定比率母线转换器在电池回收厂的高温环境下实现可靠的高功率电压转换。
从供电网络的角度来看,电池回收过程会产生大量热量。因此,供电网络的组件必须能够在高温下可靠运行。同样,在供电网络设计中,功率密度也变得越来越重要,需要小巧的外形设计和高效的电源转换。
固定比率转换器提供了一种功率密度极高的 DC-DC 转换解决方案,能够在很小的外形设计中支持数千瓦的功率和数百伏的电压。
例如,Vicor BCM6123 固定比率母线转换器的功率密度高达 2352 W/in³(见图 7)。凭借这种功率密度,设计人员就可以轻松满足电池回收厂的温度和性能要求。随着功率需求的不断增长,采用固定比率转换器的模块化电源架构使系统能以最小的消耗进行相应扩展。
图 7:Vicor BCM6123 固定比率母线转换器模块在 61.0 x 25.14 x 7.26mm 的 ChiP™ 封装中提供 24V 的输出电压和 62.5A 的输出电流。
在电池生命周期的每个阶段,对高效、高功率密度且可扩展的高压供电网络的需求都在不断增长。整个电池生命周期的成功取决于每个阶段的成功。无论是电池化成、测试、实际应用还是回收,整个电池生命周期都可以受益于固定比率转换器。与传统的电源转换解决方案相比,固定比率电压转换器有着前所未有的效率和小巧的外形尺寸,同时还具有双向转换等独特功能。
Vicor 是提供高密度固定比率转换器的唯一公司。Vicor BCM 产品采用正弦振幅转换器(SAC™)拓扑架构,比基于 PWM 的解决方案工作频率更高。BCM 系列固定比率转换器还提供多种外形尺寸和功率等级,可以满足各种高压应用的需求。除了 BCM 系列,Vicor 还提供多种固定比率转换器来满足许多其他应用的需求。
BCM 固定比率转换器将在目前快速增长的电池制造市场上扮演重要角色。它支持更高的吞吐量,效率更高,并且可以根据任何应用的需求进行扩展。无论在应用或生命周期的哪个阶段,固定比率电源转换器都是蓬勃发展的当代电池行业的理想解决方案,而传统电源转换方法目前已无法满足需求。
Vicor 和 BCM 是 Vicor 公司的注册商标;ChiP™ 和 Sine Amplitude Converter™ 是 Vicor 公司的商标。
本文最初由 Bodo's Power Systems 发表。
David 负责管理 Vicor 公司品牌形象、促销活动和企业传播等各种营销活动,并主导推动工业业务部门的收入。Krakauer 拥有麻省理工学院颁发的电气工程学士和硕士学位,以及麻省理工斯隆管理学院(MIT Sloan School of Management)的 MBA 学位。
David Krakauer,全球市场营销副总裁
从派克峰到 Bonneville 盐滩,Lightning 的速度超越内燃机摩托车
Lightning Motorcycle 设计的电动摩托车在各个领域都表现出色。了解 Vicor 电源模块如何支持下一代摩托车的详情
Vicor 展示了电动汽车高压转换至 SELV 的创新方案
高密度模块缩小了供电网络,提高效率以及改善整体性能
高密度功率模块简化和缩小电动汽车电源系统设计
Vicor 电源模块为电动汽车应用注入创新。了解三款汽车级新产品将如何彻底改变未来的电源设计
高密度电源模块推动主动悬架技术日趋成熟
主动悬挂系统已从 20 世纪 90 年代的测试版发展成为今天的 48V 驱动系统。了解电源模块对电源系统设计的影响