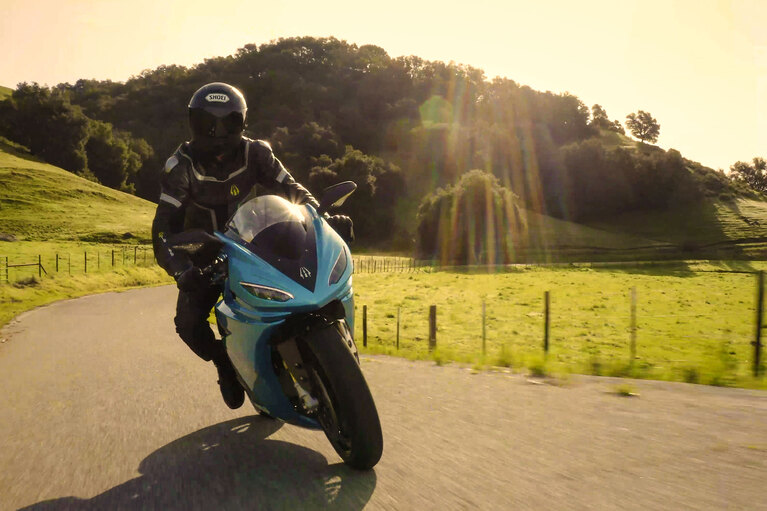
从派克峰到 Bonneville 盐滩,Lightning 的速度超越内燃机摩托车
Lightning Motorcycle 设计的电动摩托车在各个领域都表现出色。了解 Vicor 电源模块如何支持下一代摩托车的详情
在全球范围内,商业航空仍以 4.3% 的速度增长。这带来了许多好处,但对环境的影响也非常严重。了解如何使用高密度电源模块和创新的架构来减少排放,降低能耗,从而减轻这种影响。
作者:Patrick Kowalyk,汽车首席现场应用工程师
随着汽车行业向电动汽车(EV)转型,设计工程师在开发底层电气架构时面临诸多挑战。例如,800V 牵引电机逆变器中的大电容负载需要专用的预充电电路,以避免会损坏元器件的浪涌电流。
与此同时,电动汽车设计师不断努力减小系统的尺寸、减轻重量和降低成本。他们面临的挑战是,如何设计出既稳健可靠又能将设计工作量和成本降到最低的电气架构。要实现这一平衡,工程师需要考虑新的电源系统设计方法。
借助高密度电源模块,工程师就可以设计创新的架构,在与车辆预充电相关的各种因素间实现完美平衡。而固定比率转换器模块是开发最高效的预充电系统的关键。
电动汽车的运行离不开四个主要组件:牵引电池、DC-DC 转换器、牵引电机逆变器和电机。在这个结构中,电池为牵引电机逆变器提供高压(800V)直流电源,而逆变器又提供交流电来驱动电机。
从牵引电池向牵引电机逆变器供电带来了安全和可靠性方面的挑战。牵引电机逆变器偶尔会接收大电流,因此需要集成大容量的直流支撑(DC-link)电容器以保持稳定的直流供电。在许多车辆中,总直流支撑电容可能高达约 58,000µF,形成了巨大的电容负载。
在车辆启动时,这些电容未充电(0V),直接将驱动电池连接到驱动电机逆变器会导致很大的浪涌电流。当电池线路的电阻为数微欧姆,电池工作电压为 800V 时,根据欧姆定律,流经的电流(以安培为单位)如下:I = (800V - 0V)/R。
这种大浪涌电流会给系统带来安全风险,包括导致接地故障、设备损坏和保险丝熔断。此外,与直流支撑电容充电相关的高 dV/dt 可能会导致振铃和元器件损坏。
图 1:在车辆启动时,牵引逆变器的直流支撑电容充电会导致很大的浪涌电流,可能会损坏设备。
为了解决这些问题,电动汽车采用预充电电路,作为在车辆启动过程中限制浪涌电流的基本手段。
大多数电动汽车通过在牵引电池和牵引电机逆变器之间使用专用接触器和限流电阻来完成预充电(如图 2 所示)。在预充电过程中,SW1 断开,而 SW2 和 SW3 闭合。在这种模式下,车辆通过串联电阻 R1 对直流支撑电容进行预充电,有效地限制了浪涌电流。当直流支撑电容的电压达到 800V 时,预充电完成,SW3 断开,SW1 闭合,使车辆可以在正常条件下运行。
这种预充电方法确实有效,但远非理想选择。它的一个主要缺点是需要使用额外的元器件,包括一个坚固但笨重且昂贵的预充电接触器。在空间、重量和成本至关重要的电动汽车中,这些额外的组件并不受欢迎。
另一个挑战是,使用高压母线进行预充电,容易导致与过热相关的故障。例如,在短时间内多次重复启动和关闭车辆,会导致预充电电阻长时间处于电流过大的状态。这种重复的功率消耗会导致电阻过热,使系统面临短路和故障风险,而且有可能损坏高压电路。要保护预充电电路,需要专用的安全电路,而这样就会进一步增加系统的物料(BOM)、重量和成本。
图 2:在预充电期间,专用接触器 SW3 在电池和逆变器之间连接一个串联电阻。预充电完成后,SW3 断开,SW1 闭合,重新将电池连接到逆变器。
Vicor 的 BCM® 系列固定比率转换器提供了一种独特的电压转换形式,带来了一种新颖、更有效的预充电方式。
固定比率转换器是非稳压隔离式 DC-DC 转换器,峰值效率可达 98%。它们类似于交流变压器,根据转换器的匝数比或 K 因数完成固定比率降压或升压(如图 3 所示)。最重要的是,它们支持双向转换,也就是说,同一个模块可以根据电流流动的方向进行升压或降压。
图 3:固定比率转换器根据电流流动方向以预定的比率对直流电压进行升压或降压,整个过程非常高效。
在电动汽车预充电场景下,固定比率转换器的价值在于它们能够以独特的方式,利用低压母线完成预充电。
所有电动汽车都使用两块电池:主牵引电池(工作电压为 400V 或 800V)和低压电池(工作电压为 12V 或 48V)。在车辆关闭时,由低压电池为低压辅助设备(如收音机和系统控制)供电。当车辆启动后,牵引电池通过专用的 DC-DC 转换器和稳压器为辅助低压设备供电(如图 4 所示)。所有电动汽车都进行这种转换,这通常通过开关模式电源转换器等单向解决方案实现。
图 4:同时使用固定比率转换器和稳压器,就可以在预充电期间使用低压电池进行预充电,而在正常运行期间使用牵引电池为低压母线供电。
有了固定比率电源转换器模块,电源系统设计师就可以设计有效的预充电方法,既无需额外的元器件,又不增加成本或重量。
设计师可以使用固定比率转换器,从低压电池对牵引电机逆变器的直流支撑电容进行预充电,而不需要直接通过牵引电池进行预充电。在这种设计中,用于从高压母线为低压母线供电的标准 DC-DC 转换器被固定比率转换器(如 Vicor BCM6135)和 DC-DC 稳压器(如 Vicor PRM3735)所取代。重要的是,元器件总数量与原始实现方法相比保持不变。
在预充电过程中, SW1 和 SW2 处于断开状态,完全断开与牵引电池的连接。在这种模式下,PRM3735 对来自低压电池的 48V 电压进行调节,然后由 BCM6135 升压至 800V,对牵引电机的直流支撑电容进行预充电。PRM3735 的输出电流是可控的,因此这种架构可以在预充电过程中避免不受控制的大浪涌电流。
预充电完成后, SW1 和 SW2 随后闭合。利用固定比率转换器的双向转换功能,同一个固定比率转换器和 DC-DC 稳压器现在可以变换极性,将来自牵引电池的 800V 降压至 48V,为低压母线供电。
这种方法可以带来多方面的明显优势:
随着从燃油车向电动汽车的转型不断推进,对更经济、小巧、轻便的电源系统的需求日益增长。要满足这一需求,必须采用创新的方法,设计更有效的电动汽车供电网络。
凭借高效的固定比率转换器,Vicor 为电源系统设计师带来了前所未有的设计灵活性和全新的架构选项。利用现有组件进行预充电,只是展示固定比率电源转换器模块强大功能的一个例子。展望未来,随着电源系统进一步发展并成为汽车中不可或缺的组成部分,固定比率转换器将帮助打造更可持续、更经济的未来汽车。
本文最初由 Power Systems Design 发布。
Patrick Kowalyk 从事汽车电源系统研发已有 6 年多的时间,而且是一位拥有数十年实践经验的工程师。Patrick 拥有深厚全面的技术知识,为推动 Vicor 的汽车业务发展做出了重大贡献。他精通电源模块、拓扑结构和架构方面的技术,在业内可谓无人能及。Kowalyk 一直致力于帮助 OEM 厂商和顶级供应商客户设计紧凑、高效的电源系统。他毕业于伊利诺伊理工学院,获得了电气工程学士学位。
Patrick Kowalyk,汽车业务首席现场应用工程师
从派克峰到 Bonneville 盐滩,Lightning 的速度超越内燃机摩托车
Lightning Motorcycle 设计的电动摩托车在各个领域都表现出色。了解 Vicor 电源模块如何支持下一代摩托车的详情
Vicor 展示了电动汽车高压转换至 SELV 的创新方案
高密度模块缩小了供电网络,提高效率以及改善整体性能
高密度功率模块简化和缩小电动汽车电源系统设计
Vicor 电源模块为电动汽车应用注入创新。了解三款汽车级新产品将如何彻底改变未来的电源设计
高密度电源模块推动主动悬架技术日趋成熟
主动悬挂系统已从 20 世纪 90 年代的测试版发展成为今天的 48V 驱动系统。了解电源模块对电源系统设计的影响