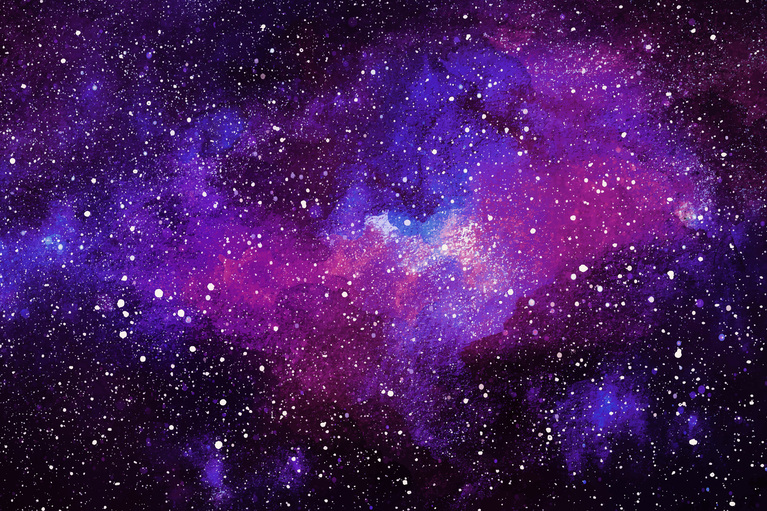
Microgate and Vicor partner to unlock deep space secrets
Learn how high density power modules help colossal Earth-based telescopes enhance deep space images
白書
電源システムの設計は、電子装置を設計する上で必ずしも重要とは考えられていません。多くの場合、完成品の電源装置を購入するか、ディスクリート部品を使って自ら設計するかという選択になります。このホワイトペーパーでは、これらの2 つのアプローチの問題点を考察し、最新の電源コンポーネントを用いた、様々な用途に対応するソリューションを説明します。
電源システムは、電子装置を設計する上で他の要素とは異なります。電源システムは、必要な機能を提供するのではなく、必要な機能を提供するコンポーネントにエネルギーを供給します。このような役割であるために、電源システムは一種の消耗品として扱われ、電子装置全体の重要性に比べてほとんど注意が向けられることがなく、仕様に合わせて市販品を選択することで済まされてしまいます。
最近の調査によると、エンジニアは多くのサブシステムを設計する必要があり、電源システムはその中のごくわずかな部分です(設計時間の4 分の3 以上を電源システムに費やしているエンジニアはわずか12% です)。彼らの設計の大部分は、デジタルシステムであることが多く、アナログの世界である電源システムとは大きく異なります。そのため、自社開発のリスクを避けて標準電源を用いることは非常に魅力的に思えますが、トラブルが発生した場合、再設計のための労力とコストがかかります。このような想定外のコストと遅延は、しばしば「電源システムの隠れたコスト」と呼ばれます。
単純なシステム、特に要求仕様が厳しくない場合は、オープンフレームの標準的な電源(いわゆる「シ ルバーボックス」)などの市販の電源を用いて、迅速に設計を完成することができます。しかし要求 仕様が厳しい場合は、単純なソリューションを使うと問題が発生する可能性があります。システム の要求仕様に厳密に一致する市販のソリューションはみつからないことが多いため、性能について 妥協するか、コストが増加して多くのスペースを占める可能性のある、オーバースペックの 製品で我慢するしかありません。
厳しい要求や規格の認証が必要な場合は、市販の製品では対応できない電気的な性能が必要になることがあります。とりわけ、航空宇宙や防衛の用途ではこの傾向があります。
要求が厳しくない用途でも問題が起こり得ます。例えば、標準のオープンフレームの電源システム で安全規格を満たすには、感電を防ぐ措置が必要です。このように保護筐体の取り付けが必要にな れば、市販の製品を使用するメリットが減少します。
問題の原因が電気的な要求仕様ではなく、動作温度などの環境的な制約によることもよくあります。たとえば、システム内部の温度は、一般に周囲よりも高温になるので、システムの動作温度に対応した仕様の電源装置でも、高温の環境では、ファンやヒートシンクで冷却しなければ、故障する可能性があり、コストやシステムサイズの増加につながります。
衝撃や振動などの機械的ストレスも、市販の電源装置の故障原因になります。標準品は、一般に機械的ストレスに耐えるように設計されていません。特に輸送用機器など、動作する環境そのものが物理的ストレスとなる例も多くあります。製造システムの制御機器など、機械的ストレスが少なくても少しの振動が信頼性に影響する場合もあります。
電源システムを設計するエンジニアは、これまでディスクリート部品を使用してきました。この設計プロセスは時間がかかるため、電源設計の幅広い経験がなければ、プロジェクトのリスクになります。技術的にも難しいために、コストが増える可能性があり、設計作業が増えると、製品の発売が遅れ、販売機会を失うこともあります(「プロジェクト遅延が及ぼす影響」を参照)。
設計開始後の要求仕様の変更は、企業の収益に大きな影響を及ぼします。要因は次の2 つです。
米国では、技術者の作業は一般的に1 時間あたり100 ~ 150 ドルで評価されるため、設計変更の時間を短縮することで、かなりのコスト節約になります。開発中のシステムによっては、製品の発売の遅れが収益に大きな影響を及ぼすこともあります。特に製品を最初に市場に出すことができれば、エンジニアリングコストも少なくなる可能性があります。
コントローラを集積したパワーデバイスとリファレンス設計を利用することで、設計は容易になりましたが、詳細設計、特にPCB レイアウトに関係して、性能が出ない状況が発生し、経験豊富な電源システムの設計者であっても、つまずく場合があります。テストや認証に合格していない電源によるリスクの増加も、このアプローチの隠れたコストになります。開発チームに高いレベルの専門知識があり、要求仕様に対して最適化が必要な場合にのみ、ディスクリート部品による設計が最適なソリューションになります。
設計者にとって最大の問題は、システム設計中の仕様変更です(Vicor が最近実施した調査では 87% の対象者が、仕様変更が重要な課題であると回答しており、67% が、ますます重大になっていると述べています)。
標準品を使用する場合、選択肢が限られており、用途が変化したときに対応できなくなることがあ ります。たとえば、追加の電源出力が必要になる場合は、システムの合計電力も増加するため、唯 一の方法は電源装置を大型化することです。ほとんどのシステムではスペースに制約があるため、 電源装置を大型化すると、元々十分なスペースを確保している場合でも、収まらなくなる可能性があります。
ディスクリート部品による設計の電源システムの場合、仕様変更の問題はさらに大きくなります。このアプローチは基本的に時間がかかるため、設計作業の開始後に仕様が変更されると、設計変更のために多くの追加の作業が発生し、予算やスケジュールが超過して、コスト増につながる場合があります。
この問題の解決策は、ロバストな手法を取り入れることです。一見基準を満たすように見える標準品を選ぶのではなく、本当に必要なものを慎重に検討し、要求仕様の想定外の変更に柔軟に対応できるようにする必要があります。これこそが、開発サイクルの後段で発生する、コストと作業の増大を防ぐ唯一の方法です。
このアプローチを用いると、市販の電源装置を使う方法では、選択肢が非常に少ないことがすぐにわかります。すべての要素を考えると、独自の電源システムを開発することが最適という結論になるでしょう。
ある顧客の製品では、2 つのセンサーを使用してDNA 分析の測定をしていました。これまでは、ファン冷却方式のディスクリート部品の電源装置を使用していました。ディスクリート部品の電源装置から、PFM、AIM、ZVS 降圧レギュレータなどの電源コンポーネントを使用した設計に切り替えることで、電源システムサイズは161cm2 から64cm2 になり、60% もの小型化ができました。
開発中に、センサーの数を2 つから4 つに増やすことに決まりました。このため、4 つのセンサーの電源で必要な電流が2 倍になり、総消費電力が200W から350W に増加しますが、電源システムのサイズは同程度に維持する必要がありました。
この顧客はVicor の電源コンポーネントを用いる設計手法に切り替えることで、サイズの増大を6% の67cm2 に抑えて、増加した電力に対応できるようになりました。同等のディスクリート部品によるソリューションでは346cm2 が必要でした。
モジュール型の電源コンポーネントを使用することは、「両者の長所を生かす」バランスの取れたソリューションです。ディスクリート部品による設計と異なり、電源コンポーネントは使いやすいため、電源装置の専門知識やリソースが限られていても簡単に使用できるだけでなく、市販の電源装置よ
りもきめ細かいレベルで電源システムを設計できるため、用途に応じたカスタマイズができます。電源コンポーネントは柔軟性に優れているため、ディスクリートや市販品によるソリューションよりもはるかに少ない労力で、要求仕様の変更に対応できます。
Vicor の電源コンポーネントを用いる設計手法とオンラインツールを組み合わせることで、電源システムの迅速な設計、分析ができます。多くの場合、市販の電源装置を選択するより時間はかかりません。Vicor の電源コンポーネントを用いる設計手法はロバストな手法です。電源コンポーネントを柔軟に使うことで、要求仕様が変更された場合のプロジェクト中断を最小限に抑えることができるため、設計後の段階で問題が発生することがなくなります。
Vicor の電源コンポーネントを用いる手法には、電源に関する高度な専門知識は必要ありません。電源コンポーネントは、最小限の周辺回路を追加するだけで連携して動作するように設計されているためです。これまでディスクリート部品により設計していた、または、市販の電源を選んで使っていた設計者が、電源システム設計の隠れたコストを減らすために、Vicor の電源コンポーネントを用いる設計手法に切り替えています。
Microgate and Vicor partner to unlock deep space secrets
Learn how high density power modules help colossal Earth-based telescopes enhance deep space images
高性能電源モジュールで、世界最先端の完全電動ワーククラス ROV (eWROV) を実現
Saab UK社は、小型で放熱性の高い電源モジュールを使って、世界最高クラスの性能をもつ、環境に優しい eWROVを実現
Powering Innovation eBook: Volume 1 – Saving the environment
Technological breakthroughs to protect and preserve the environment
Powering Innovation eBook: Volume 2 – Protecting and saving lives
Innovative solutions that protect and deliver lifesaving materials and services