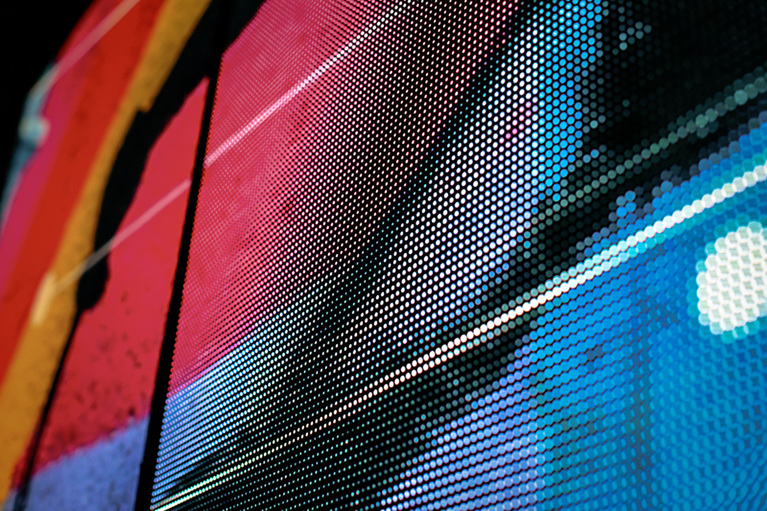
Light, efficient LED power design uses 48V and power modules
LED displays are getting larger, more expensive and more costly to operate. Vicor power dense modules are smaller, lighter and more efficient to run
To optimize commercial LED displays, there are a few fundamental questions that must be considered.
By Author, Tom Curatolo, Principal Technical Sales Engineer
LED technology has advanced by leaps and bounds in the last decade, in many cases displacing LCD technology. We are most familiar with the changes we have seen as our consumer televisions have gotten progressively thinner, lighter yet larger and more energy efficient. But even more significant advancements have been made with exterior lighted displays that are being used for digital signage. These vibrant and captivating commercial displays dwarf smaller format consumer units and consume far more power. So, the overall system architecture and power delivery network is a critical part to the design of these systems.
Direct-view LED video wall technology has become a very popular choice for large-scale displays because of its superior brightness and color uniformity as compared to liquid crystal display (LCD) technology. However, large-video displays present a daunting power design challenge – how best to develop an efficient solution that reduces energy losses, minimizes heat generation, is easily scalable and safe? Heat can be a big problem with light emitting diodes (LEDs). More heat results in excessive temperatures, which rapidly degrades LED luster and longevity.
One factor contributing to the heating of a LED panel is the heat losses in converting and distributing power within the video wall; losses both from the power converters and the resistive copper losses in cabling and the printed circuit board. So, what’s the solution? Evaluating the merits of different partitioning options will help identify the best option when designing high-powered LED application.
In addition to being brighter, direct-view LED displays are considerably more power-efficient than LED backlit LCD displays because they can produce more light output using less energy (i.e., “useful power”). Nonetheless, they still generate a significant amount of “wasted power” in the form of heat. This may seem surprising as LEDs are typically cool to the touch. That's because they don't generally produce heat in the form of infra-red radiation, which is detectable by touch. In fact, up to 85% of the energy consumed is dissipated as heat so large-scale LED arrays demand significant power in excess of that converted to light.
For large LED panels the LED power dissipation can become significant. For example, In Las Vegas the “Fremont Street Experience” display consumes 2.2MW (megawatts) at full brightness and requires even more energy by day to combat the effects of the bright Nevada sunlight. Even small displays have large numbers of LEDs and consume significant power: for example, a display module from one leading manufacturer contains an array of 80 x 80, i.e., 6,400 total LEDs and requires 300W (5V, 60A).
Maximizing efficiency is, therefore, essential in the design of an LED power supply.
Large-panel video LED displays, composed of multiple smaller panels, need to be capable of being powered from a common bus voltage. Distributing Alternating Current (AC) directly to each panel and converting the AC to DC conversion on each panel would be too costly, too bulky and is generally not an option for safety reasons. Instead, a single bulk AC-DC converter stage would be recommended to supply an isolated low-voltage bus voltage to power each individual panel. With large panels, the distance from the bulk AC-DC supply to the LED drivers can be many meters in length, which creates challenges as power levels increase making it an important design consideration.
Heat is the primary enemy of LEDs and inherent inefficiencies in the power design can only exacerbate the situation. Excessive thermal conditions shorten the useful life of an LED and causes discoloration. Even worse, the light output declines with increasing junction temperature; an efficient power-supply system for LED use must pay attention to each individual component to avoid local hotspots, which can result in LEDs that not only fail faster, but look dimmer throughout their operating life. This is especially critical in a video wall where not only light quality, but color uniformity is important.
Transmitting power from the power supplies to the LED array over resistive copper wires incurs power losses in the form of heat, known as distribution losses. The distribution loss for a current (I) is proportional to the square of the current and is given by P = I2R, where R is the resistance of the wire, bus bar or PCB trace; reducing it requires either reducing the current or reducing the resistance of the wire.
Reducing the current while delivering the same total power to the load requires increasing the voltage (P = VI). Doubling the voltage, from 24 to 48V for example, reduces the current by 50%, which in turn reduces the distribution loss by 75%.
Attempting to achieve the same result by reducing the wire resistance requires quadrupling the conductor cross-section area, which adds weight and cost and is not very practical.
Another way to dissipate power losses is to minimize the number conversion stages. For example, removing a conversion stage can improve system efficiency by 5 – 10% and depending on the power level can reduce the amount of heat generated into the system. To eliminate a conversion stage a designer needs to select components that can offer high step-down conversion ratios without compromising efficiency.
The most commonly used bus voltages used to power LED panels has been 24V and 12V. Compared to distribution AC, it removes potentially lethal voltages from the panels and they meet the Safety Extra Low Voltage (SELV) “safe” voltage level for low voltage power supplies.
However, a superior option to 12V or 24V is to double the intermediate voltage to 48V. Since 48V is below 60V it still meets the SELV safety criteria, even including an overvoltage protection allowance of 20%. Compared to a 24V system, this cuts the currents by half for a given power level and reduces cable cost and weight which equates to greater savings!
By increasing the bus voltage to 48V you can cut your distribution losses up to 75%, which dramatically reduces heat generation. A lower operating temperature improves system reliability and lower current reduces the thickness of the LED panels. Busing a higher voltage with lower distribution losses also allows the video wall to be more efficient and reliable which helps to reduce the overall lifetime operating costs for the end user.
Power modules are the most effective way to create a compact power delivery network. Modular designs invariably provide a smaller, lighter approach to power system design. Power modules encapsulate many components into a single planer package. The planer design delivers better thermal performance and make designing easier and more scalable. Vicor power modules are the most power-dense modules on the planet and are highly efficient, lightweight and compact. When hanging heavy, commercial LED signs, weight and high-performance are essential.
The answer is quite simple, if we can look beyond the accepted norm of using power systems that rely on 12V and/or 24V intermediate bus voltages and just double the bus voltage to 48V, the benefits are both immediate and sustainable over the lifetime of the equipment:
Leveraging 48V bus make all the difference when designing high power, large-scale LED displays. This reduces cable weight significantly. Add that benefit with modular power design and you have the opportunity to cur long-term power consumption, deliver brighter LEDs and drastically reduce the weight of your power delivery network.
This article was originally published by Power Systems Design.
Tom Curatolo is a Principal Technical Sales Engineer supporting the Aerospace and Defense sector. Tom has more than 40 years of experience in the high-tech electronics industry with specific expertise in power electronics and power architectures. He has been with Vicor Corporation for more than 30 years. The majority of his time with Vicor has been in Applications Engineering where he has extensive experience in supporting the diverse customer base and markets that Vicor products address. Tom received a B.S. degree in Electrical Engineering from Worcester Polytechnic Institute in 1985. Tom is based in Andover, Massachusetts.
Tom Curatolo, Principal Technical Sales Engineer
Light, efficient LED power design uses 48V and power modules
LED displays are getting larger, more expensive and more costly to operate. Vicor power dense modules are smaller, lighter and more efficient to run
Vicor partners with Voltserver™ for Digital Electricity™
Digital Electricity enables operators to safely transmit as much 2kW of power across 2km using off-the-shelf data cabling. Vicor delivers DC-DC conversion
Digital electricity brings intelligence and safety into power transmission
Digital Electricity™ offers the benefits of low-voltage with the power and distance capabilities (2km) of AC. Vicor provides DC-DC power conversion
モジュール型設計の強み(英)
Power delivery networks are rapidly changing, and their power requirements require a wide portfolio of modules to enable the maximum.