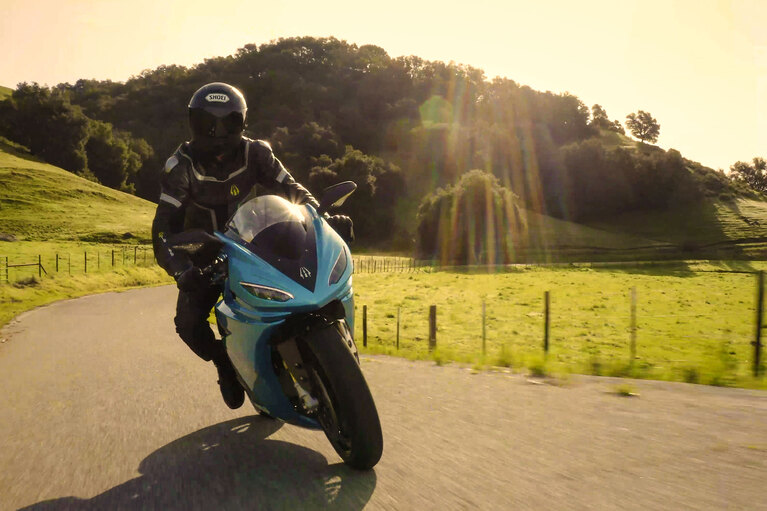
從派克峰到 Bonneville 鹽灘,Lightning 的速度超越內燃機機車
Lightning Motorcycle 設計的電動摩托車在各個領域都表現出色。瞭解 Vicor 電源模組如何支持下一代摩托車的詳情
White paper by Ian Mazsa, Director of Product Marketing
The power architectures of pure electric (EV) and hybrid vehicles store and distribute power at a mix of voltages to power a wide variety of sensing, control, safety and infotainment subsystems. This presents a cost, space and weight challenge for the power storage and power delivery network, which hybrid vehicles solve with a 48V battery and 48V distribution system, but EVs solve with high voltage batteries (800V, 400V) and a 48V distribution system. While a 48V battery can instantaneously supply the required power, any intermediate battery in EV architectures adversely affects weight, space and cost.
The opportunity to innovate within EV power architectures is to use a high voltage battery to preserve the advantages of high-voltage energy storage while also removing the need for an intermediate battery by using a DC-DC converter to deliver power within a SELV range. A conventional converter can provide the voltage conversion but lacks the fast response time required to meet the power drawn by the wide variety of subsystems. The Vicor BCM® presents a low path impedance and fast response time, transforming the high voltage battery into what appears as a 48V battery to the power delivery network, eliminating the need for an intermediate 48V battery.
This white paper details the Vicor BCM converter’s function, operation and capabilities as compared to a conventional DC-DC converter, and suggests an architectural implementation when used in an EV power architecture.
EV power architectures are complex compared to previous architectures, due to a variety of subsystems that have both dynamic and static power levels at both legacy 12V and new 48V inputs. To avoid the additional cost and weight of an intermediate energy storage stage, a converter with fast transient response and high efficiency is needed to convert the high voltage battery into voltages that can be safely distributed throughout the vehicle.
The BCM converter operates as a fixed ratio converter where the output voltage (also called secondary side voltage) is a fixed fraction of the input voltage (also called primary side voltage). That fixed fraction can be greater, equal or less than one; call this fixed fraction the K factor, defined as the voltage at the input divided by the voltage at the output (VSEC/VPRI). When the K factor is less than one, input voltages scale down but input currents scale up. When the K factor is greater than one the input voltages scale up and input currents scale down.
Conceptually, the internal operation of the BCM converter has three stages:
Functional block diagram of BCM converter: Even though it converts DC to DC, the BCM uses a transformer to convert AC to AC at high efficiency, scaling the magnitude by the K factor and using the switching blocks to convert between AC and DC. The switching is done at a high frequency and due to the transformer like energy transfer the conversion has a fast response to transient load changes and presents a low impedance path between input and output.
The switching stages switch at the zero-current, zero-voltage crossings of the sine wave in the transformer, which minimizes the losses due to switching. Due to the symmetry and with the appropriate sequencing and control it is possible operate the BCM as either a step down (high to low conversion) or a step up (low to high conversion). This innate bidirectional capability enables the BCM to convert power with the same efficiency in either direction. This creates possibilities for power conversion in applications where there is rapid charging and discharging from a storage element for example. For the purpose of this article, the focus will be on the high to low conversion application.
Utilizing zero-current, zero-voltage switching (ZCS/ZVS), the BCM converters operate at higher frequencies than conventional converters. For example, the BCM6135 operates at 1.2MHz and unlike a conventional ZV/ZC resonant converter, the BCM operates within a narrow band frequency. The BCM high-frequency operation provides a fast response to changes in load currents and a low impedance path from input to output. Fixed ratio conversion, bidirectional operation, fast transient response and a low impedance path are the set of qualities that enable the BCM to make a 384V battery appear like a 48V battery — which we will term transformation. This ability to transform a power source is both the key benefit and key difference when compared to conventional converters.
The BCM transforms an input voltage into an output voltage by a fixed ratio scaling, and can be mathematically expressed as the operation VOUT = K • VIN. Consider a 48V power distribution system drawing power from a high voltage battery charged to 384V. The loads on the 48V bus have an input voltage range that is a fixed fraction of the output of the battery. An isolated BCM (1/8) converts the output of the HVDC battery into a range of voltages compatible with 48V distribution. Due to the fast< response time of the BCM — from the perspective of any load on the low side — the 384V battery appears like a battery discharging at 48V. The BCM converter has effectively transformed the high voltage battery, allowing the overall system to incorporate all the advantages of a higher voltage battery for energy storage — such as faster charge time and improved energy density — compared to a 48V< battery of equivalent energy storage.
Transformation of a high voltage battery: When a 1/8 K factor BCM converts the output of a 384 V battery, a 48V virtual battery is created. This conversion preserved the 384V battery's energy density and transient power delivery capability but at a SELV voltage compatible with downstream distribution.
Now consider the same application but with a conventional converter, which regulates the input in the voltage range to a specific output voltage that is decoupled from changes on the input. Voltage fluctuations on the input do not propagate to the regulated output. The low bandwidth of the regulated converter prevents the distribution system from delivering power as quickly as a direct connection to the battery. From the point of view of the low side, there is only an idealized 48V supply voltage. While there is utility in this conversion, recognize two relative weaknesses. First, the lower bandwidth necessitates some additional intermediate energy storage (either capacitive or an extra battery) to supply current during a high dI/dt discharge event. Second, a regulation stage is unnecessary because the input voltage of the loads on the low side, are a fixed fraction of the battery on the high side. The conventional converter is needlessly regulating – wasting energy, adding cost, and reducing overall system efficiency. In addition, the limited bandwidth of the regulated converter degrades the reaction time to fast power draws in the distribution system.
By designing the voltage range of a power source to be a fixed fraction of the input range of loads in the power distribution, high voltages — with the associated benefits of low path losses — can be used to distribute power without unnecessary regulation stages used in systems with conventional converters. Going further, designing a system where all voltage ranges, for sources, loads, and various distribution paths are fixed ratios of each other allows optimal selection of the best in class technology for power storage, power distribution, and subsystem capabilities. This is achieved in high-performance EV power architectures. These systems use Li-ion batteries arrayed for capacity and high-voltage for fast charging time, distribute power at 48V per the LV148V specification for SELV power distribution, and use a mix of legacy 12V cost-effective subsystems alongside the latest 48V powered AI technology. BCMs bridge all these voltages into a single high efficiency system.
Decoupling of a 48V source from a high-voltage battery: When a conventional converter creates 48V from a battery, the lower bandwidth of the converter cannot deliver power as quickly and also expends energy in an unnecessary regulation stage.
EV power architectures can use BCMs to create a high efficiency and lightweight power system. The high voltage battery arrays, which are the primary energy storage unit, are stepped down (high to low conversion) to the most efficient voltage to distribute power. The high voltage array has advantages — energy density and charge time, compared to lower voltage arrays — but also drawbacks (not SELV) that make it desirable for EV applications but dangerous for distributing power to loads throughout the vehicle. Instead, implementing a power distribution system to the LV148 spec allows power to be distributed at a safe voltage (SELV) that could be more easily maintained than the high voltage from the battery, and would require less copper for lower current than if it had been distributed at the legacy 12V.
The BCM converter reflects the HV battery discharge characteristics scaled by the K factor 1/8. This virtual battery powers the LV148 compatible distribution system as effectively as any physical 48V battery, but with the energy density and associated benefits of a high voltage battery in the system.
EV power architecture: With a much lighter weight but the same energy storage, a 384V battery can be used like a 48V virtual battery by using a BCM. EV power architectures can distribute 48V power and use NBMs to integrate legacy 12V subsystems into the more efficient and lightweight architectures.
The Vicor BCM6135 converter is isolated, providing the required protection when interfacing a high voltage source to a SELV distribution, and has over 97% peak efficiency with over 96% efficiency when operating over 30% of rated current. Capable of delivering up to 65A (over 3000W) of power continuously, arrays of BCM6135 converters can create high power conversion stages between HVDC and SELV voltage ranges. The BCM6135 has an input range of 260 – 410V and a fixed ratio conversion of 1/8 to deliver an output compatible with 48V distribution.
The BCM6135 measures 61 x 35 x 7.5mm, has chassis mount or through-hole mounting options and weighs 68g. Its high power density (3400 W/in3) facilitates physical placement where optimal for the power architecture and weight distribution within the vehicle. The package is designed to operate in both conduction and liquid cooled systems, and has roughly equivalent thermal dissipation on the bottom and top side of the package to give further flexibility in mounting and cooling solutions.
BCM6153 efficiency over output load current
While system power can originate from a 48V virtual battery, it still must be distributed throughout the vehicle to a broad assortment of subsystem loads that with different power requirements and a mix of 48V and legacy 12V inputs. While the advantages of delivering power at 48V vs. 12V are clear (higher efficiencies and lighter cables) how this mix will change over time is not. As 12V is marginalized, the vehicle power architecture must be flexible enough to adapt to new subsystems while still optimizing the weight and cost of all the required cabling.
The ideal solution is to extend the 48V distribution as far as physically possible and convert to 12V for legacy needs only where and when needed. Since the LV148 specification operating range can be transformed to a 12V distribution compatible input with a 1/4 K factor conversion, a BCM converter is the ideal solution for maximizing efficiency. Furthermore, since both voltages are SELV, isolation is not needed and a non-isolated converter can be used to convert 48V to 12V throughout the system. Identical in all other features, a non-isolated BCM is called an NBM and has all the same benefits previously described: fast transient response, low impedance and bidirectional operation.
This distributed power architecture gives all the benefits of 48V distribution while maintaining flexibility for the platform to adopt new subsystem as needed with either 48 or 12V inputs. The NBM transforms the 48V input into what appears as a 12V source to the 12V legacy systems. It can be integrated ubiquitously in the vehicle; it’s physically small enough to augment existing legacy subsystems wherever they are already placed yet also minimally disruptive if removed for future system upgrades to native 48V subsystems.
NBM2317 efficiency over output load current
The Vicor NBM2317, measuring 23 x 17 x 7.4mm and weighing 12g (less than half an ounce), can be placed wherever optimal for extending 48V distribution. Peak efficiency is over 97.5% when operating over 30% of rated current. Capable of delivering up to 60A (800W) of power continuously, the NBM2317 is designed for optimal flexibility in cooling through either the top or bottom side with a surface mount compatible package that can fit into an existing layout with minimal disruption. The high power density (4500 W/in3) is beyond competitive modules, while also more integrated than any discrete solution at an equivalent power level.
Used together, the BCM6135 and NBM2317 provide the flexibility for EV power architectures to adopt the optimal mix of 48V and 12V subsystems, while maximizing the advantages of SELV 48V distribution and HVDC power storage to achieve the vision of high-performance EV designs.
The capability of BCMs to transform power sources, especially a battery, is both the key benefit and the key difference when comparing BCMs to conventional converters. Provided the power architecture’s primary power supply output voltage is a fixed ratio to any downstream subsystem input voltage, power can be distributed at the highest optimal voltage and then converted as needed by BCMs without the losses due to unnecessary regulation stages. The benefit realized for EV architectures is the elimination of any intermediate battery due to the transformation of the high voltage energy storage battery into a compatible SELV range for delivery throughout the vehicle. While both BCMs and NBMs are finding homes in EV power systems, any other system powered from a battery, from ultralight UAVs to autonomous factory robots to artificial intelligence computing platforms at the edge, can take advantage of their transformative capabilities.
從派克峰到 Bonneville 鹽灘,Lightning 的速度超越內燃機機車
Lightning Motorcycle 設計的電動摩托車在各個領域都表現出色。瞭解 Vicor 電源模組如何支持下一代摩托車的詳情
Vicor to present at the EEHE Conference on electronics in hybrid and electric vehicles 2025
Power dense DC-DC converter modules and Sine Amplitude Converter enable top system performance and downsizing for the most challenging power use profiles
Vicor 展示了電動汽車高壓轉換至 SELV 的創新方案
高密度模組縮小了供電網路,提高效率以及改善整體效能
高密度功率模組簡化和縮小電動汽車電源系統設計
Vicor 電源模組為電動汽車應用注入創新。瞭解三款汽車級新產品將如何徹底改變未來的電源設計