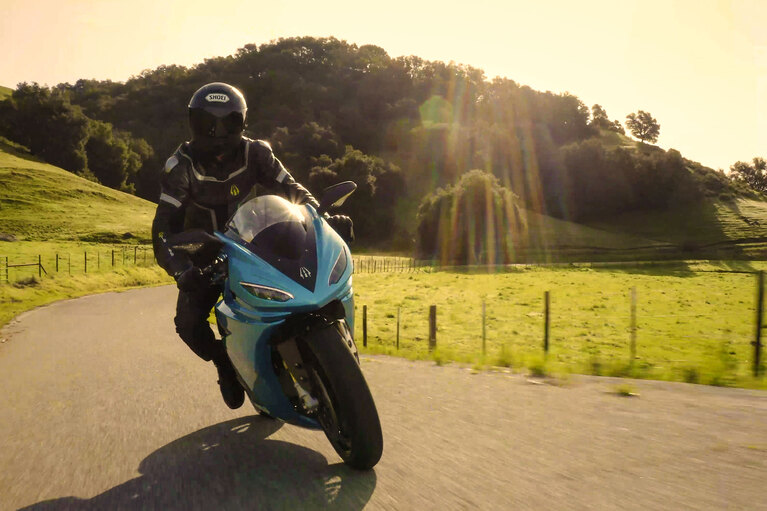
从派克峰到 Bonneville 盐滩,Lightning 的速度超越内燃机摩托车
Lightning Motorcycle 设计的电动摩托车在各个领域都表现出色。了解 Vicor 电源模块如何支持下一代摩托车的详情
The pace of automotive electrification has never been more aggressive and focused. To achieve their demanding goals, OEMs need to innovate like never before. They need to explore the impact of a modular power design.
Electric vehicles currently constitute about 11 percent of global vehicle production, a total that is expected to jump to 62 percent by 2030. About half are expected to be fully electric.
Credit Suisse projects about 63 million new vehicles worldwide by the beginning of the next decade, with an estimated 29 being all-electric. Industry observers note that growing power demand will further strain electrical grids.
In an interview, with Patrick Wadden, vice president of Vicor Corp.’s Automotive Business Development unit, stressed the need for strong investment in electrification and power technologies that will play a key role in solving powertrain efficiency challenges.
“Volvo is claiming that 50 percent of their vehicles will be electric, and the remaining ones are going to be hybrid by 2025. By 2030, Ford, GM and Chrysler are going to be investing over $50 billion. This year new vehicle estimates are even higher than last year,” Wadden added.
Figure 1: By 2030, battery electric vehicles (BEV) will account for 45% of all xEVs (Source: Credit Suisse estimates).
Car makers are electrifying some of their most popular vehicles, including the new Ford Mach E (the electric Mustang) and its flagship F150 truck, dubbed Lightning. The new vehicles include fast-charging technology while promising lower maintenance costs.
Electric power levels in cars with internal combustion engines typically range from 600W to 3kW. New EVs require power levels ranging from 3 to 60kW, or up to 20 times that of conventional vehicles. The increase represents a major challenge for power engineers trying to optimize power delivery networks. To meet those challenges, Wadden emphasized the need for lightweight, compact systems offering flexibility so power components can easily scale and be reused across fleets.
To maximize vehicle electrification, OEMs must increase power levels, reduce powertrain size and weight while improving thermal management and reusability. The choice of powertrain and charging is critical. Manufacturers are striving to optimize their power networks by investing millions of dollars in electrification R&D while iterating with new technology. For example, 48V power supply technology is rapidly expanding, both for fully electric and hybrid vehicles.
OEMs need to pack as much power as possible into a constrained space. “Vehicles need compact and efficient power solutions,” said Wadden. To achieve full-fleet electrification, OEMs need to be able to reuse designs across different platforms to speed deliveries. Scaling is essential when modifying power levels among sedans, minivans and SUVs that share the same platform.
Overall vehicle weight affects performance, particularly battery life. Vicor is pitching a modular bus converter (BCM6135) billed as providing 98-percent efficiency via electrical interference filtering, decreased cooling and a 25kg 48V battery replacement case. The 61-by-35-by-7mm power module converts the primary battery from up to 800V to 48V, delivering more than 2kW of power with a power density of >4.3kW/in3.
Figure 2: Power delivery networks using power modules reduce size and weight.
As vehicle electrification advances, design teams increasingly must consider changing power requirements. Wadden said a scalable, modular power system allows designers to implement standard approaches in a variety of EV powertrains. Modularity also allows distributed power architectures using a 48V bus. Power modules can be placed in alternate locations for localized 48V/12V conversion – for example, in a glove compartment, trunk or near each wheel.
Wadden added that qualification of vehicle electronic components represents a common delay in development. Delays can run up to three years. Hence, high-density power modules are promoted as reducing design qualification times.
“Innovation is needed in the form of new architectures and topologies that provide maximum performance today and can also be reused and reconfigured for the future,” said Wadden. “Integration is important. If you look at one of our modules that has 200 individual components inside, it’s a lot easier to qualify one module than it is 200 components. And so integration has a lot of merits.”
Many EVS are now using 800V primary batteries to meet the required power levels and deliver higher performance. Existing converters are bulky due to the high input-to-output voltage (800V to 48V) ratio. Fixed-ratio conversion modules like Vicor’s, operating at high switching frequencies, offer efficiencies of up to 98 percent, thereby reducing system size and weight. Decentralized architectures and modular power supplies for the distribution of the 48V power can help simplify designs.
Vicor automotive modules also can be connected in parallel. With the addition of a few others components, it is possible to boost a power delivery network from a few hundred watts to tens of kilowatts.
Power modules deliver distinct advantages, promising higher power density, flexibility and faster power system design.
This article was originally published by EE Times.
从派克峰到 Bonneville 盐滩,Lightning 的速度超越内燃机摩托车
Lightning Motorcycle 设计的电动摩托车在各个领域都表现出色。了解 Vicor 电源模块如何支持下一代摩托车的详情
Vicor 展示了电动汽车高压转换至 SELV 的创新方案
高密度模块缩小了供电网络,提高效率以及改善整体性能
高密度功率模块简化和缩小电动汽车电源系统设计
Vicor 电源模块为电动汽车应用注入创新。了解三款汽车级新产品将如何彻底改变未来的电源设计
高密度电源模块推动主动悬架技术日趋成熟
主动悬挂系统已从 20 世纪 90 年代的测试版发展成为今天的 48V 驱动系统。了解电源模块对电源系统设计的影响