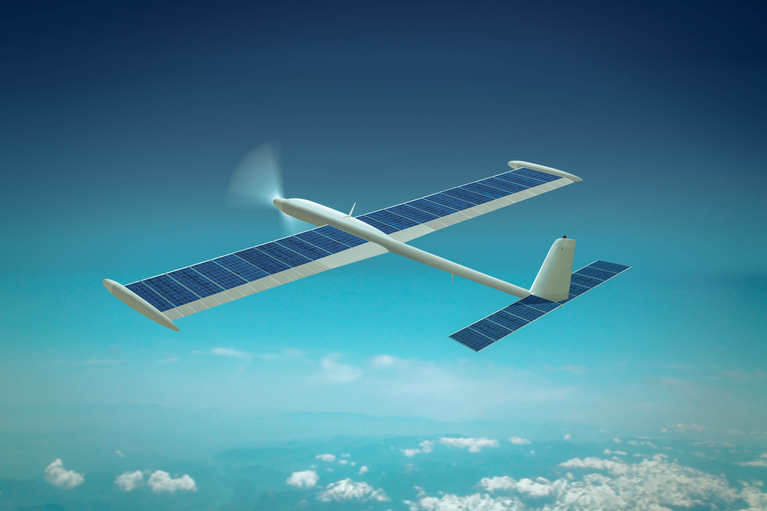
High-efficiency, high-density modules free up space for advanced communications and extend range
High-efficiency class of UAV depend on solar power to meet its long flight time requirements
White Paper by Chester Firek
A high-level overview of power trends in the high-power LED market
Direct-view LED video wall technology is becoming an increasingly popular choice for large-scale displays because of its superior brightness as compared to LCD technology. However, large-video displays present a power design challenge – how best to develop an efficient solution that reduces energy losses, minimizes heat generation and is easily scalable? Heat can be a big problem with LEDs. More heat results in excessive temperatures, which rapidly degrades LED luster and longevity.
One factor contributing to the heating of a LED panel is the heat losses in converting and distributing power within the video wall; losses both from the power converters and the resistive copper losses in cabling and the printed circuit board. So what’s the solution? Evaluating the merits of different partitioning options will help identify the best option when designing high-powered LED application.
Figure 1: What happens in Vegas... the Fremont Street Experience LED display has 7,552 x 552 pixel resolution with a 2in pixel spacing and consumes 2.2MW at full brightness. With 12.5 million LEDs, it measures 1,500 x 90ft (Image courtesy of Indianapolis Museum of Art).
In addition to being brighter, direct-view LED displays are considerably more power-efficient than LED backlit LCD displays because they can produce more light output using less energy (i.e., “useful power”). Nonetheless, they still generate a significant amount of “wasted power” in the form of heat.This may seem surprising as LEDs are typically cool to the touch. That's because they don't generally produce heat in the form of infra-red radiation, which is detectable by touch. In fact, up to 85% of theenergy consumed is dissipated as heat so large-scale LED arrays demand significant power in excess of that converted to light.
For large LED panels the LED power dissipation can become significant. For example, the Fremont Street Experience display (Figure 1) consumes 2.2MW at full brightness and requires even more energy by day to combat the effects of sunlight. Even small displays have large numbers of LEDs and consume significant power: for example, a display module from one leading manufacturer contains an array of 80 x 80, i.e., 6,400 total LEDs and requires 300W (5V, 60A).
Maximizing efficiency is, therefore, essential in the design of an LED power supply.
Large LED arrays composed of multiple panels can provide seamless images of any size or shape, with excellent viewing characteristics from all angles. Examples range in size from a simple scrolling message display to displays like the Fremont Street Experience shown in Figure 1, with 12.5 million LEDs. Figure 2 shows two display examples where LED technology has unique advantages: a taxi‑mounted LED advertising display and a highly-curved display around the side of a building.
Figure 2: LED displays can change in response to real-time vehicle location information (left) or conform to three-dimensional shapes (right).
The power-supply system must convert incoming AC voltage to isolated low voltage, high-current DC in the most efficient way. Each stage of power conversion adds cost and wastes energy, so minimizing the number of stages is a design priority.
Large video walls are composed of many modules linked together, so an efficient design must also scale well with minimum duplication of power-conversion stages.
What are two of the key design priorities?
Figure 3: Relative light output vs. junction temperature of different-colored LEDs (Image source: RPI/LumiLeds).
A simple way to improve power-system efficiency is to minimize the number conversion stages. For example, removing a conversion stage can improve system efficiency by 5 – 10% and depending on the power level can reduce the amount of heat generated into the system. To eliminate a conversion stage a designer needs to select components that can offer high step-down conversion ratios without compromising efficiency.
There are a number of ways to partition a power-supply system to convert AC mains to low-voltage DC for the LED drivers and control circuits. No matter which particular partition is selected, a typical design will include the following blocks:
For example (Figure 4), Vicor offers a comprehensive portfolio of products to simplify the design of power supplies for large-scale video walls. The result is a simple design that minimizes conversion stages and requires few external components.
Figure 4: A mixed-voltage AC-DC power system partitioning. The PFM outputs the intermediate bus voltage to PoL converters at each panel.
Vicor structures a high-efficiency approach for high-powered LEDs as follows:
AC Input Stage: The AC Input Front-End Module (AIM™) performs line rectification, EMI / RFI filtering, transient protection and inrush limiting to provide a non-isolated, rectified AC line voltage to subsequent stages.
AC-DC Conversion: The PFM™ family comprises isolated & regulated AC-DC converters with PFC for AC-DC systems. The AIM / PFM combination is capable of converting a universal AC to an isolated 48 or 24V with efficiency of up to 92% for systems up to 400W; in a form-factor smaller than an average smartphone (Figure 5). The family features a double-sided thermal housing with chassis- or board-mounting options.
Figure 5: Standard smartphone next to a 4414 VIA™ PFM™.
DC-DC Buck Conversion: Cool-Power is a family of high input-voltage, wide-input-range DC-DC Zero-Voltage Switching (ZVS) buck regulators that integrate controller, power switches and support components into a single package. The ZVS topology enables megahertz switching frequencies which reduce gate drive losses and body diode conduction losses; Cool-Power ZVS regulators can operate from either 12, 24 or 48V inputs and achieve efficiencies of over 97.5% and requires only an external inductor and minimal capacitors to form a complete DC-DC buck regulator solution.
Using the building blocks previously mentioned, there are several possible system partitions for an LED video wall.
Large-panel displays, composed of multiple smaller panels, need to be capable of being powered off a common bus voltage. Distributing AC directly to each panel and converting the AC to DC conversion on each panel would be too costly, too bulky and is generally not an option for safety reasons. Instead, a single bulk AC-DC converter stage is typically used to supply an isolated low-voltage bus voltage to power each individual panel. With large panels, the distance from the bulk AC-DC supply to the LED drivers can be many meters in length, which creates challenges as power levels increase.
24 and 12V power distribution have been the most commonly used bus voltages for LED panels. Compared to distribution AC, it removes potentially lethal voltages from the panels and they meet the SELV (Safety Extra Low Voltage) “safe” voltage level for low voltage power supplies.
However, a superior option to 12V or 24V is to double the intermediate voltage to 48V (Figure 6). Since 48V is below 60V it still meets the SELV criteria, even including an overvoltage protection allowance of 20%. Compared to a 24V system, this cuts the currents by half for a given power level and reduces
cable cost and weight – more savings!
It also cuts distribution losses by 75%, which reduces heat generation. A lower operating temperature improves system reliability and lower current reduces the thickness of the LED panels. Busing a higher voltage with lower distribution losses also allows the video wall to be more efficient which reduces the lifetime operating costs for the end user.
Generating an isolated 48V bus to distribute can be very simple, in addition to the AC input PFM™ a high-powered three-phase AC-DC converter could be followed by a Vicor Bus Converter Module (BCM ) to convert 380V to an isolated 48V with peak efficiency up to 98%. A single high-voltage BCM is capable of 1.75kW of power delivery within 63 x 22mm size, 2,735W/in3 power density. Either 48V solution can then be followed by a 48V input Cool-power buck or buck-boost regulators to directly power LEDs or LED drivers.
Figure 6: 48V power-system architecture.
So how do you deliver brighter LEDs that last longer?
You explore the merits of several approaches first. Driving thousands of LEDs in a large-scale video display requires an efficient power system to produce the low-voltage, high-current supply needed. Traditionally designers have turned to a PoL solution that uses 24V as the intermediate DC voltage. Increasing the voltage to 48V though, reaps numerous benefits that 24V just can’t deliver:
To safeguard your next large-format LED display deployment – keeping them brighter, longer – start with 48V.
Vicor in LED
Vicor modular power-system components help designers easily assemble configurable, high-density LED power supply systems that are highly efficient. Because the component system is inherently flexible, it works for virtually any power level, size or form factor, with minimum effort. By combining flexible, high-efficiency building blocks with intuitive online design tools and easy-to-use development kits, designers can optimize power-system designs with speed and ease.
High-efficiency, high-density modules free up space for advanced communications and extend range
High-efficiency class of UAV depend on solar power to meet its long flight time requirements
High-density, high-power modules enable lighter, safer, lower cost tether cables to extend missions
This class of unmanned vehicle is powered and controlled via a tether from a ground-based power source assisting in extended missions
DCM DC-DC converters double the internal bus power and help keep the aircraft as light as possible
High-altitude long-endurance (HALE) UAVs are essentially flying satellites, designed to operate at extremely high altitudes for extended periods
Extend flight times and support high-performance surveillance equipment to ensure safety and security
Effective surveillance requires uninterrupted sensing and communication to ensure the safety and security of valued property, equipment, and assets