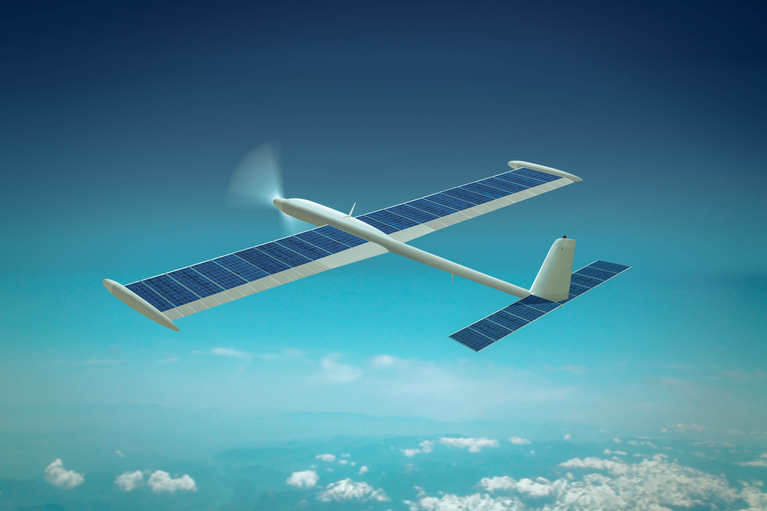
High-efficiency, high-density modules free up space for advanced communications and extend range
High-efficiency class of UAV depend on solar power to meet its long flight time requirements
Longer run times and range make long distance humanitarian missions possible using Vicor power modules.
Power delivery networks (PDNs) based on high-density power modules from Vicor are enabling the use of hydrogen fuel cells in drones, where size, weight and efficiency are critical. New hydrogen power technology is paving the way for mobile robot development with extended range and load capacity. Doosan Mobility Innovation (DMI) has now successfully used hydrogen-powered drones to deliver humanitarian aid in remote locations that require up to two hours of flight time.
In addition to delivering humanitarian aid, the long run-time of DMI’s drones allows them to be used for commercial monitoring. DMI has demonstrated this by monitoring the vast area of one of Korea’s largest solar power plants where conventionally powered drones would have required more than six battery changes.
Figure 1: Example of solar panel inspection (Source: Doosan Mobility Innovation)
Achieving DMI’s success was dependent not only on their innovative approach to hydrogen power, but also on their use of Vicor high-performance, high-density power modules to deliver power from the fuel cell battery to the various loads within the drone.
A power delivery network (PDN) is the design of power elements, wires and harnesses that delivers power from the source to the loads in a system. The choice and architecture of a PDN is a system-wide decision and has a significant impact on the drone design and its capabilities. DMI, working with Vicor, chose to use a 48V system which is quickly becoming a standard in many applications to improve efficiency and reliability.
The 2.6kW DP30 power supply system used by DMI has two main groups that supply power to the drone rotors and controllers for the two stacks. Due to the wide range and variable output voltage of the DP30 power supply, from 40 to 74V, the output power units operate at 48V, 12A for the motors and at 12V, 8A for the control circuits and fans. The structure is supported by a Vicor PRM™ buck-boost regulators and a ZVS buck regulator (PRM48AF480T400A00 400W buck-boost regulator / PRM48AH480T200A00 200W buck-boost regulator).
“Wide range of fuel cell voltage and the hybrid connection to the conventional Li-Po battery is the key configuration of our power management system. By doing that, it allows the lithium batteries to automatically charge by Fuel Cell when needed, or discharge when Fuel Cells need additional power when the drone is operating. Thermal management is important to hydrogen fuel cell, and we have an inner cooling fan to regulate the heat,” said Jiwon-Yeo.
The increased flight time, coupled with rapid refueling, opens a wide range of new business possibilities for companies using drones for offshore platform inspection, search and rescue operations, high-quality aerial photography, precision agriculture, deliveries and more.
ZVS Buck switching regulators offer board-level designers maximum power density and flexibility for high-efficiency point-of-load DC-DC regulation. The integration of a high performance Zero-Voltage Switching (ZVS) topology increases point-of-load performance, providing best-in-class power efficiency up to 98%. The ZVS Regulators are highly integrated with control circuitry, power semiconductors and support components, in a high density System in Package (SiP). The device can also be configured to operate in constant current mode.
ZVS Buck switching regulators
This article was originally published by EETimes.
UAV solutions: Increasing payload capability and flight times of commercial UAVs
Case study: New class of tethered drones revolutionizes maneuverability and remote communications
Article: Design guide to powering tethered UAVs
Vicor PRM™ regulator PRM48AF480T400A00
Vicor PRM™ regulator PRM48AH480T200A00
High-efficiency, high-density modules free up space for advanced communications and extend range
High-efficiency class of UAV depend on solar power to meet its long flight time requirements
High-density, high-power modules enable lighter, safer, lower cost tether cables to extend missions
This class of unmanned vehicle is powered and controlled via a tether from a ground-based power source assisting in extended missions
DCM DC-DC converters double the internal bus power and help keep the aircraft as light as possible
High-altitude long-endurance (HALE) UAVs are essentially flying satellites, designed to operate at extremely high altitudes for extended periods
Extend flight times and support high-performance surveillance equipment to ensure safety and security
Effective surveillance requires uninterrupted sensing and communication to ensure the safety and security of valued property, equipment, and assets