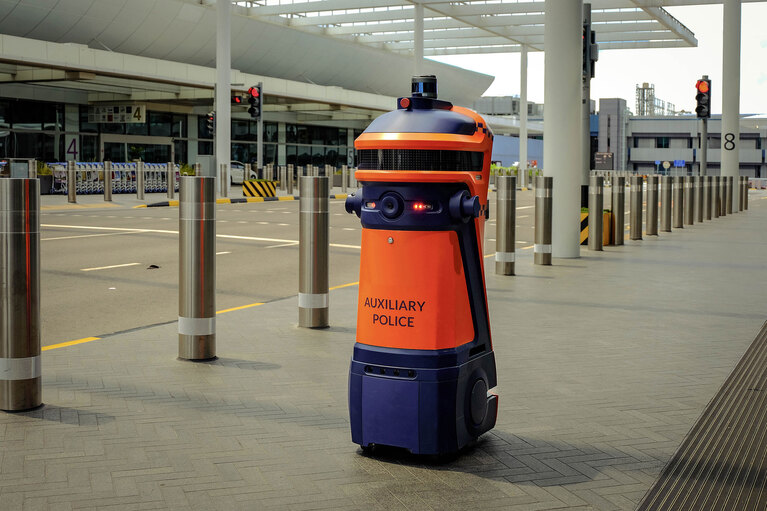
Compact power modules allow space for advanced sensors that improve security and performance
Inspection robots can monitor infrastructure more frequently and allow for rapid remediation before problems occur, saving lives, time, and money
Managing power conversion with a mixture of Vicor modules helps to accelerate the design process by ensuring reliable operation across diverse operating and temperature ranges – both indoors and outdoors.
By Myra Espinola, Business Development Manager
Figure 1: Dusty eliminates the conventional, labor-intensive process of physically transferring building plans onto the floor with a robot programmed at the job site to automate the same task.
Figure 1: Dusty eliminates the conventional, labor-intensive process of physically transferring building plans onto the floor with a robot programmed at the job site to automate the same task.
Innovations in power conversion technology are enabling a transformation in robotics design. Today’s integrated power modules address the demanding size, weight, power budgets and cost efficiencies required to move robots from factory, residential and commercial applications into a vast new landscape bounded only by the imagination.
We are hitting a tipping point where robots are bringing tremendous benefits to our lives. Some robots take orders in restaurants, others work security and still others operate on constructions sites adding precision to floor plan layouts. Robots are everywhere. And OLogic is a big reason for why we see this proliferation.
OLogic, Inc., a Santa Clara, CA electronics consultancy, has more than 15 years of experience helping its clientele bring robotics designs to market in both large and small volumes by providing electrical, mechanical and industrial engineering support, as well as software and firmware engineering. This includes expertise in power electronics integration, which is a prime design consideration that determines the range, functionality and charging capacity of mobile robots.
“I think the big reason people contact us is because they need help with the electronics design in the robot they’re going to build, and we uniquely understand that need because we’ve built dozens and dozens of robots,” said OLogic CEO, Ted Larson. “You could hire an individual engineer who has worked at a robotics company, or you could hire someone to manage us, and your whole project will succeed.”
OLogic has designed scores of robots across many industries including agriculture, smart homes and inventory control to name a few. OLogic traces its robotics customer base to a start-up considered by many to be the progenitor of mobile robotics in Silicon Valley. Willow Garage was noted for its ability to tie together off-the-shelf, open-source software from universities and other entities to help robots perform difficult tasks.
When the company disbanded in 2014, it triggered a diaspora of robotics software experts who subsequently founded nearly every important robotics start-up in the Bay Area. This opened new business for OLogic with companies such as Savioke, Knightscope, Fetch and Dusty Robotics.
“The real rock stars of the robot industry are the ones doing high-level software for things like machine learning or robot algorithmic task navigation,” Larson said. “The electronics are kind of an afterthought. What happens is that people think they can get away with buying all this off-the-shelf stuff and then plug it together. It turns into a house of cards really quickly.”
Mobile robots have unique power challenges. Sensors, servo motors, actuators, data servers, communications systems and other devices that operate the robot have different power and power density requirements. Some are power-hungry. Others may operate infrequently. This demands the ability to provide power quickly, cleanly and cost-effectively from a battery-power source.
Vicor Corporation has introduced OLogic to a modular approach to building power delivery networks (PDNs) for robots. Vicor high-density power modules have enabled high-efficiency power conversion that easily scales, making it very adaptable.
“The parts we’ve been using most lately are the Vicor ZVS Buck Regulators,” Larson said. “We use them everywhere on mobile robots now. I don’t ever have to think about, ‘Oh, I need five or ten amps at 12 volts, so I’m going to go build my own supply.’ I don’t ever think that way anymore.”
One customer working closely with OLogic to optimize its power profile is Dusty Robotics (Dusty). Based in Mountain View, CA, Dusty builds robot-powered tools for the modern construction workforce.
For centuries, the construction industry used two simple tools to lay out building floor plans: a tape measure and a chalk line. Even today, when architects design buildings using sophisticated 3D CAD models, the process still calls for the layout to be printed on paper, hauled onto the job site and manually transferred to the ground. The tape measure and marker process are slow and prone to human error that impacts schedules and budgets. Errors cause rework, which typically account for 10% of a cost of a construction project, according to Dusty.
“When plans are laid out by hand, a lot of mistakes are made, actually a lot more than the construction industry is even aware of,” said Philipp Herget, co-founder and CTO of Dusty Robotics. “We’ve heard of cases where layout mistakes have bankrupted construction companies. We prevent those types of mistakes from happening because everything is marked correctly – not by hand, by a robot.”
Dusty eliminates the conventional, labor-intensive process of physically transferring building plans onto the floor with a robot programmed at the job site to automate the same task. The Dusty FieldPrinter robot loads a digital version of the floorplan and then prints the layout on the ground for features such as walls, doors, plumbing and electrical chases. And it does so roughly five times faster than a human and to within one-sixteenth of an inch to spec.
This innovation helps the construction industry operate more like a digitized manufacturer, increasing consistency, predictability and reliability while improving working conditions for the skilled craftspeople who are at the heart of the building process. Dusty also helps improve efficiency when builder’s piece together prefabricated building panels, which is an increasingly common construction option. Unlike hand-built walls, for example, which can be adjusted on the fly, pre-fab construction materials are designed to come together only one way, which can compound errors if they are installed incorrectly.
OLogic robot image
Figure 2: Dusty FieldPrinter helps the construction industry operate more like a digitized manufacturer, increasing consistency, predictability and reliability while improving working conditions for the skilled craftspeople who are at the heart of the building process.
“If you can reduce the amount of time that’s allocated in your schedule, you can speed up how quickly the building is going to be put up,” Herget said. “And the sooner the building completes, the sooner you can start collecting revenue. Time is money. Speed has a tremendous value in the construction industry.”
Dusty’s FieldPrinter is a battery-powered mobile robot that operates for long periods in a variety of weather conditions. It includes many different electronic devices, including sensors, drive motors and motorized components, computationally-heavy processors and a printer – all of which have different operating voltage and current requirements. Because of this, a large part of Dusty’s electronics design is dedicated to power conversion to supply power to multiple components and in an environment where the battery has a constantly changing output voltage.
This is why Dusty engaged OLogic to build the core electronics for its robot. OLogic began by using discrete power solutions. Over time, however, the company came to realize that they were unable to design something as operationally and thermally efficient and with the wide operating range as a Vicor power module. Additionally, Vicor modules, such as the ZVS Buck Regulator, are extremely cost-efficient given the power they deliver.
“Vicor’s ZVS Buck Regulators deliver 200 to 300 watts of power in a really tiny package, and they’re 97 percent efficient,” marveled Larson. “You could never design something like that from the ground up and have it work as well for the same money. There’s just no reason to not use Vicor products as a result. It’s easier than designing it discretely. It’s faster. I don’t have to validate it. And there’s less risk involved.”
Dusty’s robots are complex and require 12V, 5V and 3V rails operating at significant power levels. Managing power conversion with a mixture of Vicor modules helps to accelerate the design process by ensuring reliable operation across diverse operating and temperature ranges – both indoors and outdoors.
With a long battery life and state-of-the-art power conversion technology, Dusty’s robotics innovation is helping digitize the construction industry by creating a single source of truth on the job site, based on the digital model. Instead of the architect, general contractor and each trade partner working off of their own paper plans, everyone now builds off of the single design printed on the floor. The ability to provide a digital layout improves coordination between these myriad partners, enabling better planning, execution and faster completion.
“Construction automation is enhancing what humans can do,” Herget said. “People used to use screwdrivers, and now they use power tools. It just makes their job a lot easier. Our robot-powered tools are enabling the construction industry to level up, creating better outcomes while also improving the working environment for skilled craftspeople.”
Dusty’s story symbolizes the challenges for mobile robots today. Minimizing size and weight are important in design, but increasing power is essential supporting new sensors, peripherals and features. So using power-dense modules coupled with the expertise of OLogic are the perfect combination to drive the next-generation robotics innovation.
This article was originally published by Power Systems Design.
Myra Espinola joined Vicor in 2015. She has over 39 years of experience in electrical design engineering, business development, and technical sales and marketing. In her current role as Senior Business Manager, she is focused on growing the company’s business in the industrial market, developing key customer partnerships in the area of ATE, robotics, semiconductor manufacturing equipment, drones, battery charging, heavy machinery and light vehicles. Prior to Vicor she was with Cognimem, Baxter Healthcare and Honeywell. Myra holds a B.S. in electrical engineering from the Catholic University.
Myra Espinola, Business Development Manager
Compact power modules allow space for advanced sensors that improve security and performance
Inspection robots can monitor infrastructure more frequently and allow for rapid remediation before problems occur, saving lives, time, and money
Lightweight and efficient power modules extend delivery routes and save space to carry more goods
Last-mile consumer delivery of groceries, take-out food and online consumer items is the mission-critical task of autonomous robots
High-efficiency power modules maximize system run-time and improve productivity
Logistic robots like AMRs and AGVs provide inventory management and order fulfillment tasks within large warehouse environments
フレキシブルでスケーラブルなモジュールで構成するソリューションにより多くのシステムに対応、より健康的で清潔な空間を実現 (英)
Robots use UV lamps or disinfecting sprays to eliminate dangerous pathogens and bacteria from large areas such as schools, warehouses, hospitals, etc.