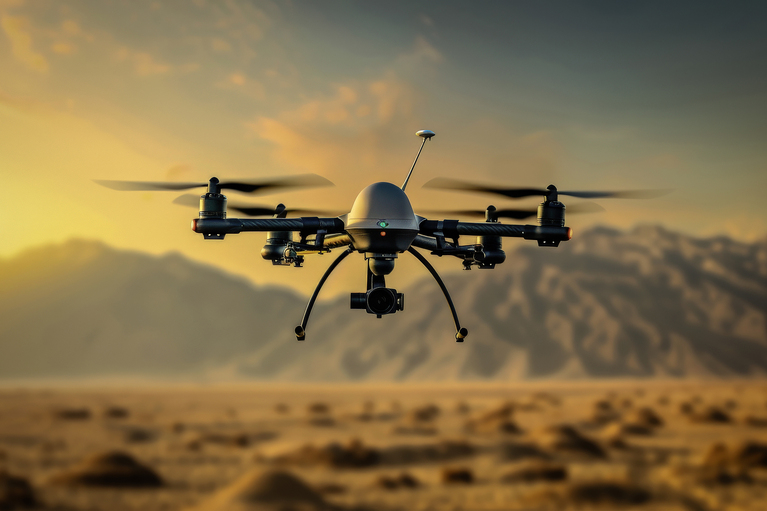
Build better UAVs using modular power
Power Delivery Networks (PDN) based on Vicor high performance power modules enable innovative designs for the next generation of UAV development
Power modules deliver the performance needed to support wireless charging that matches a wide range of impedances.
Logistics, delivery and inspection industries increasingly rely on mobile robotic fleets. These fleets have become large enough that their users are trying to find ways of recharging them that do not rely on manual intervention.
Figure 1: An aerial drone landing on a WiBotic charging pad. The WiBotic charging system automatically manages both inductive charging when the receiver sits close to the power transmitter and magnetic resonance charging for situations like this one where the receiver sits some distance from the power transmitter.
One means of automating the robotic charging process is through use of a wireless charging station developed by WiBotic. Their approach is to build wireless charging hardware into the robotic platform. The charging hardware sends the bot to a charging station when it senses the battery needs a charge. The bot positions itself near the charging station in a way that aligns transmitting and receiving coils for power transfer.
WiBotic technology incorporates both inductive and resonant systems via what’s called an Adaptive Matching system. It constantly monitors relative antenna position and dynamically adjusts both hardware and firmware parameters to maintain maximum energy transfer efficiency across several centimeters of vertical, horizontal and angular offset. An embedded identification and communication system lets any robot charge from any station, even if the robots have different battery chemistries, voltages, and charging rates.
WiBotic chargers must carefully manage charging modes to optimize up-time while not degrading batteries through repetitive quick charges. This variability in charging cycles and power levels – from 300W for fast charging to 100mW trickle-charging – also requires a power delivery architecture that matches a wide range of impedances.
To efficiently accommodate the wide range of loads, WiBotic used a Vicor zero-voltage switching (ZVS) buck-boost PRM regulator. Its topology enables a high switching frequency (about 1MHz). High switching frequency reduces the size of reactive components, enabling a power density of up to 1,383 W/in3. The Vicor regulator is integrated into the RF transmitter onboard the WiBotic TR-110 wireless charging station. The 48V input (the regulator accepts a 36–75VDC range) is from an AC-DC power supply. The output voltage is dynamically controlled and trimmed from approximately 20 to 55V as needed.
Figure 2: Visible on the TR-110 wireless charging station PCB are the cooling fans that dissipate heat from the onboard RF amplifier. The Vicor surface-mounted PRM (not visible) sits outside this airflow.
The Vicor PRM™ handles full-charge and trickle-charge modes with no significant drop-off at lower power levels — a critical performance benchmark that defeated competing power components, as well as a ‘topping-off’ mode requiring a constant voltage for a 100% charge. High-efficiency conversion yielded a maximum operating temperature of 45°C. The TR-110 wireless charging station employs active cooling to dissipate heat from the onboard RF amplifier, but the Vicor surface-mounted PRM sits outside this airflow.
The zero-cross switching of the Vicor PRM module also minimized EMI/noise challenges and conducted emission/EMC requirements with no need for additional filters.
The compact size of the PRM helps keep the onboard charger small and light weight, thus promoting long operating cycles particularly for airborne fleets. For the stationary wireless charging stations, a dense power delivery architecture ultimately helps conserve valuable real estate in the deployment environment.
The PRM is in a surface-mount package measuring 1.28 × 0.87 × 0.249in [32.5 × 22.0 x 6.31mm] which is compatible with standard pick-and-place and surface-mount assembly processes. It also provides a planar thermal interface area to enhance thermal conductivity.
PRM™ regulators
This article was originally published by Power Electronic Tips.
Build better UAVs using modular power
Power Delivery Networks (PDN) based on Vicor high performance power modules enable innovative designs for the next generation of UAV development
High-efficiency, high-density modules free up space for advanced communications and extend range
High-efficiency class of UAV depend on solar power to meet its long flight time requirements
High-density, high-power modules enable lighter, safer, lower cost tether cables to extend missions
This class of unmanned vehicle is powered and controlled via a tether from a ground-based power source assisting in extended missions
DCM DC-DC converters double the internal bus power and help keep the aircraft as light as possible
High-altitude long-endurance (HALE) UAVs are essentially flying satellites, designed to operate at extremely high altitudes for extended periods